Smart Manufacturing
Integrating city planning and industrial innovation can make our cities more sustainable for people and the planet.
Beginning in 1765, the first industrial revolution transformed our economy by using coal to change the way goods were produced and manufactured. Since then, the second industrial revolution was driven by gas in 1870 before being followed by nuclear power in 1969. Today, we are driving through the fourth industrial revolution (Industry 4.0) as we see a shift from fossil fuels to renewable energy such as solar and wind power. These revolutions show how quickly the manufacturing industry changes dependent on the source of power, with Industry 4.0 helping the manufacturing sector cut greenhouse gas emissions (GHG) from the use of renewable energy.
Use of digital data in manufacturing to cut carbon emissions
Industry 4.0 is already happening. It’s transforming the way manufacturing operations are carried out. However, the use of renewable energy is a by-product created by the drive of the digital revolution. The momentum that is shifting Industry 4.0 comes from the acceleration of digital technology. Industry 4.0 is creating cyber-physical systems that can network a production process enabling value creation and real-time optimization. The main factor driving the revolution is the advances in artificial intelligence (AI) and machine learning. The complex algorithms involved in AI use the data collected from cyber-physical systems, resulting in “smart manufacturing”.
The impact that Industry 4.0 will have on manufacturing will be astronomical as operations can be automatically optimized to produce increased profit margins. Additionally, the use of AI and smart manufacturing can also benefit the environment.
The first step to reducing emissions is always understanding. To reduce a manufacturing process’s emissions, a company must know their emissions in the first place. Thus, quantitating a baseline for GHG emissions is vital. Smart manufacturing can make this process simple by automatically collecting utility data such as electricity, natural gas and water usage. AI-based tools can also help establish Scope 3 emissions from a company’s supply chain. A smart manufacturing process will have its digital twin represented in the Internet of Things and so an entire supply chain could be modelled in the digital twin making data collection simple.
Once a baseline has been calculated, smart manufacturing can be used to reduce emissions using methods such as digital twin optimization and predictive maintenance. Each method highlights the future of smart manufacturing.

Replicating industrial processes
Digital twin optimization enables virtual replicas of industrial processes that can easily be optimized to their most efficient performance. Digital twins allow more testing and iteration creating smart strategies based on both profits and carbon reduction strategies.
Predictive maintenance can save both costs and carbon emissions by preventing unnecessary maintenance tasks. This is becoming increasingly popular as it saves companies costs in performing scheduled maintenance, or costs in fixing broken equipment. The AI-based tool uses machine learning to learn how historical sensor data maps to historical maintenance records. Once a machine learning algorithm is trained using historical data, it can successfully predict when maintenance is required based on live sensor readings in a plant. Predictive maintenance accurately models the wear and tear of machinery that is in use.
Of course businesses must first look at reducing their demand. This applies to both energy demand and reducing demand on resources such as materials and water. They can also look at reducing waste. This includes wasted energy in the form of inefficient machinery, wasted materials, and wasted water. Addressing all of these types of waste will reduce carbon emissions. Businesses will want to look at efficient maintenance scheduling; reducing time spent and spares used, increasing serviceability, decreasing downtime, making optimal use of their human resources, and optimizing any travel between sites that resources may need to undertake. Yet there are still further options to explore to become more sustainable.
Industrial synergy
One option is the use of materials that are considered waste material from one industry that could be an input material for another industry. This is also true for energy where process heat might be lost from a manufacturing facility that puts out waste heat which could be captured and used to warm a process or an area of a neighboring facility. This is known as industrial synergy. Use of, or repurposing of, otherwise wasted materials forms part of the circular economy, where materials are not thought of as waste, but are seen as resources. Industrial synergy goes further than recycling, re-using, and re-purposing within their own business by considering the wider community.
For this reason, collaboration outside of their immediate company or even their immediate town is necessary.
Initiatives facilitating industrial synergy are improving industrial waste management systems and diverting waste from landfills. They also create jobs and need a diverse network of participating companies at a high level of stakeholder buy-in.
NISP – National Industrial Symbiosis Programme is one such. Originating as 3 pilot schemes in Scotland, West Midlands, and Yorkshire & Humberside, it was the world’s first national industrial symbiosis program. The model has to date been replicated in 20 countries worldwide at a national or regional level. Participating businesses diverted 47 million tonnes of industrial waste from landfill and generated a billion pounds in new sales. Carbon emissions look cut by 42 million tonnes and money was saved by reducing disposal, storage, transport, and purchasing costs.
Cities account for more than 60% of global GHG emissions.
Source: UN Habitat
The Western Cape Industrial Symbiosis programme, WISP is based on the facilitated approach to industrial symbiosis. Initiated by the Western Cape government of South Africa in 2013, it has a team of facilitators trained by international synergies that worked full-time to build the industrial symbiosis network. They identify underutilized resources that could lead to business opportunities for member companies.
Community Resource Information Support platform, CRISP is an innovation project to design and pilot an innovative resource utilization software, and subsequently, the use of digital data to reduce carbon meets industrial synergy.
Synergy can also lead to incorporation with smart manufacturing using renewable energy without fossil fuels. This can lead us to a clearer view of the potential for clean manufacturing and a step change in low-carbon city planning.
In the context of city industrialization, not only is smart manufacturing essential but so too are the cities in which industries are located. Through innovative change, both cities and industries offer solutions for deep infrastructural and systematic carbon reductions. Within the urban context, changes in industry can lead the way in which city development and the adoption of smart technology can offer solutions to GHG reduction within cities.
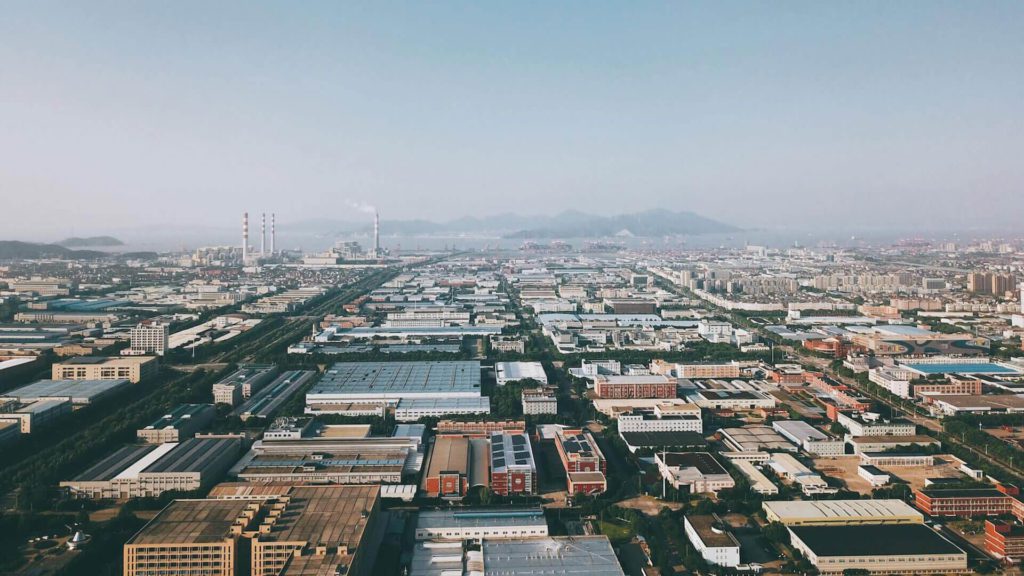
Cities account for more than 60% of global GHG emissions and contribute significantly to climate change as a result. According to the European Commission, greenhouse gas emissions can be monitored and reduced within cities through upgraded urban transport networks, upgraded water supply, environmentally friendly water disposal facilities and buildings with high energy efficiency. Sustainable Development Goals outlined by the UN recognize that cities and their contributions to climate change must be reshaped and adapted to present opportunities as opposed to threats.
The complexities of cities do require insight through a multi-governance approach to identify areas for change. Manufacturing provides opportunities both environmentally and socially towards the continued growth and development of industries.
Economically the impact of industrial manufacturing has had historical benefits towards the development of cities in drastic ways, from the employment opportunities for urban workers to the creation of goods and services that bring value to communities and infrastructure. In adapting manufacturing processes within industries, the benefits towards cities are vast, and can provide environmental, social, and governmental opportunities that showcase a more conscientious and sustainable way to live.
Public transportation, building construction, and road infrastructure can be adapted and developed in line with manufacturing industries. Workers who travel by car can instead reduce emissions and their own cost of living by making use of low-carbon infrastructure changes such as trams, buses, and trains. In developing our cities around smart manufacturing, pollution and congestion can be made a thing of the past.
To achieve these fundamental changes to cities, we must recognize the level of collaborative effort that is required between public, private, and civil actors in society. Acknowledging this is the first step to developing and creating new potential pathways for future models of cities.