Building the Circular Economy in Brussels
The traditional linear economic model is under pressure. The rapid use of natural resources is producing colossal amounts of waste and is unable to respond to many complex challenges — such as social inequality and climate change. A major solution lies in the circular economy, and the construction sector is building the way there.
The Brussels-Capital Region sees the linear model of resource extraction-production-consumption-waste as unsustainable and considers it has a harmful impact on the environment while making society highly dependent on increasingly scarce raw materials from outside the capital. Brussels also sees an opportunity to evolve towards a circular economy: one of recovering, producing, consuming and reusing. Better management of internal flows of goods will make our capital city much less dependent on external resources. It should also provide sound answers in terms of the environment, local economy and employment.
In the circular model, economic growth is no longer inextricably linked to the depletion of raw materials. It is no longer an end in itself, but a means of improving the quality of life.
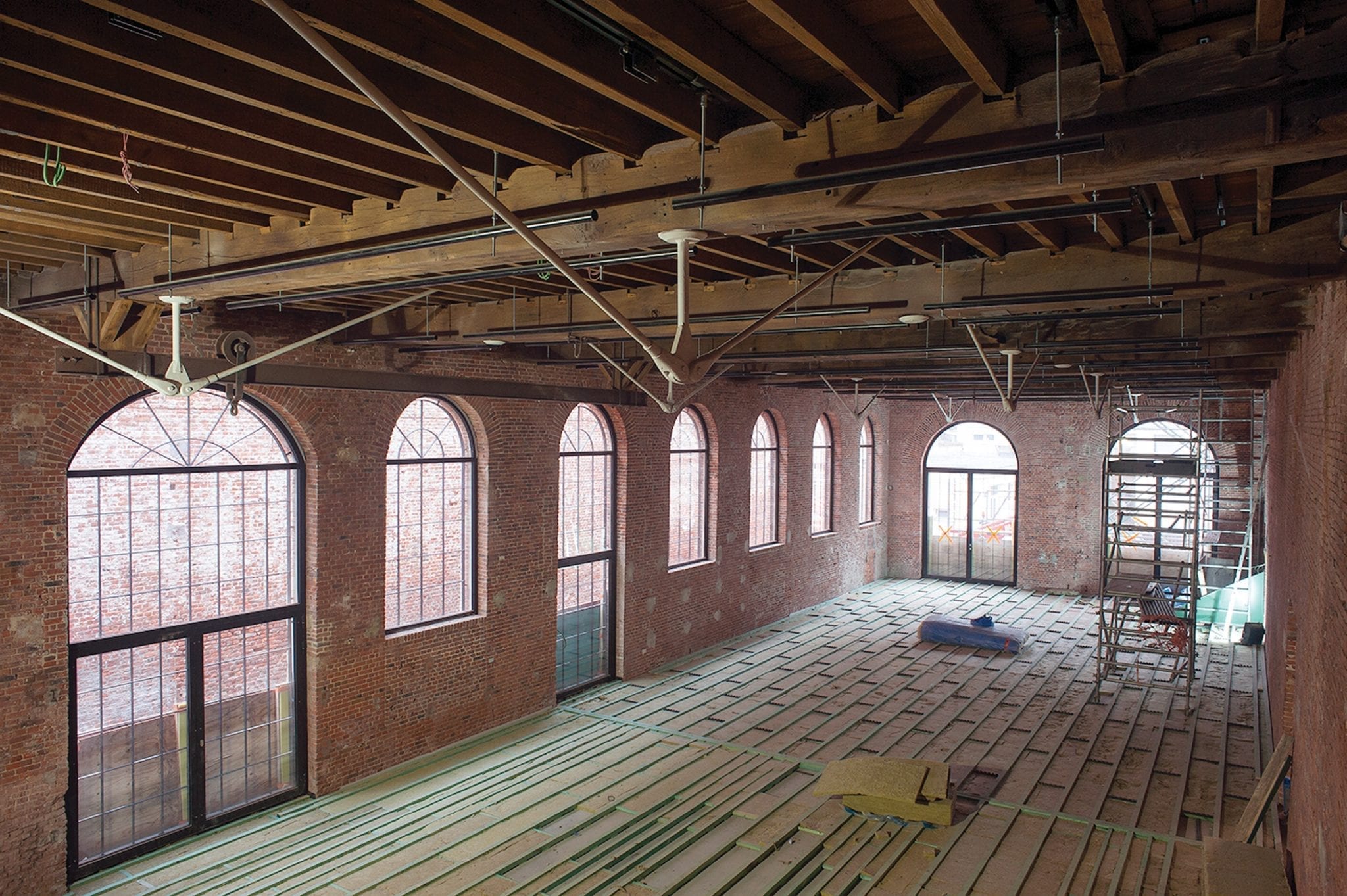
The Regional Programme for a Circular Economy (RPCE)
The Brussels-Capital Region aims to be a pioneer in Europe and that is why, three years ago, politicians launched the ambitious RPCE that brings together the different players in the region. The RPCE contains concrete actions that need to be implemented, as well as mechanisms to make it evolve over time. Three ministers and 13 partner boards are managing the plan in close cooperation with the private sector, working both bottom-up and top-down.
Local companies and independent entrepreneurs are also invited to submit ‘circular’ projects on an annual basis. Under the title “Be circular, be Brussels,” these initiatives count on financial support and guidance. And the results so far are promising: in the construction sector, Brussels’ policy-makers see a lot of potential and drive towards the circular economy. Since the start of the RPCE, no less than 21 ‘circular’ construction sites have been launched. Here, materials are reused within the region, site installations and workforces are shared, buildings are preserved as much as possible and local know-how and jobs are created.
From waste to raw materials
One of the ambitions of the RPCE is to move from waste management to raw material management in the construction sector to address the production of no less than 628,000 tonnes of waste per year in Brussels. An estimated 91% of this waste is recycled and is then used, for example, for the groundworks of roads or buildings, but this is downcycling whereby the materials irreversibly decrease in value.
Downcycling – materials are reused but decrease in value.
Upcycling – materials are reused and increase in value.
The circular economy strives for a more sustainable alternative – one that maximizes resource efficiency. Improved resource efficiency can be achieved through maintenance, reuse, and remanufacturing, and through upcycling: materials or products are recovered and transformed into materials or products with a higher quality or value. A good example is the project Tomato Chili by Dzerostudio Architects that uses formwork wood and windows – also simply known as waste from construction and renovation projects in Brussels – to build new greenhouses.
New business models, more sustainable jobs
Companies that aim to extend the life of their products will be able to pick up and overhaul previously sold products, returning the parts to the production cycle and no new raw materials will need to be produced. Companies will be able to provide products as a service, and include extra benefits such as maintenance, repair, leasing and take-back schemes. Or they will share materials, labor and buildings. Two of Brussels’ construction projects, Deswaef and Debatty deployed their trainees and site installations optimally and efficiently in this way.
New models for strategic partnership cooperation are emerging in which companies exchange information much better with other players; for example, architects and contractors can work together in so-called building teams from the design phase.
The circular scenario also has positive effects on employment. The construction sector is struggling with high personnel turnover, a shortage of skilled workers and social dumping. In the future, trainees, students and jobseekers will have a much better chance of finding and keeping high-quality jobs. Examples include drawing-up a material inventories prior to demolition, dismantling materials, preparing them for reuse, reversible design processes, and the manufacturing of new products with recovered materials.
Buildings As Material Banks (BAMB)
The RPCE plan promotes a radically new vision and approach to Brussels’ building stock. Rather than demolishing them too quickly, we can see buildings as material banks, or huge material stockpiles. Maintenance and repair, re-use, overhaul and transformation are carried out for as long as possible. Building professionals and policymakers know at any moment which materials are located where within the Brussels territory. They use inventories and material passports for this purpose. Each design is adaptable and reversible; the materials are easy to dismantle and move. All this keeps construction and demolition waste – and the use of raw materials – to a minimum.
Buildings As Material Banks (BAMB) is a project within the European Horizon 2020 programme, which promoted this new way of thinking and working in the construction sector. Starting in 2015 and ending in February 2019, BAMB was coordinated by Brussels Environment. Six pilot projects tested the materials passports, reversible building design and circular building assessment tools that were developed during BAMB. This generated insights about policies and opportunities for developing new business models. Brussels carried out 2 of the 6 BAMB pilots.

Build Reversible in Conception (BRIC)
The BRIC building is built, deconstructed and reconstructed entirely by young trainees of the EFP Training Center in Brussels. It was designed as a materials bank and will have three different functions in three years’ time. The concept is therefore adaptable and reversible; the materials are easy to assemble and disassemble. The first version, BRIC 1, was a 70m2 office. More than 180 students participated in setting up and dismantling this module. The rebuilding of BRIC 2 into a 130m2 trading space is under construction and will be finished in June 2019. And in 2020, BRIC will be transformed one last time.
The circular economy strives to maximize resource efficiency.
The fact that this is a sustainable way of building is now apparent. In the dismantling of BRIC 1, only 3.5m3 of waste was generated, a lot less than what was expected. And there’s more good news: if each version of this building were to last 20 years, the greenhouse gas emissions from the reuse of materials could be reduced by 50%.
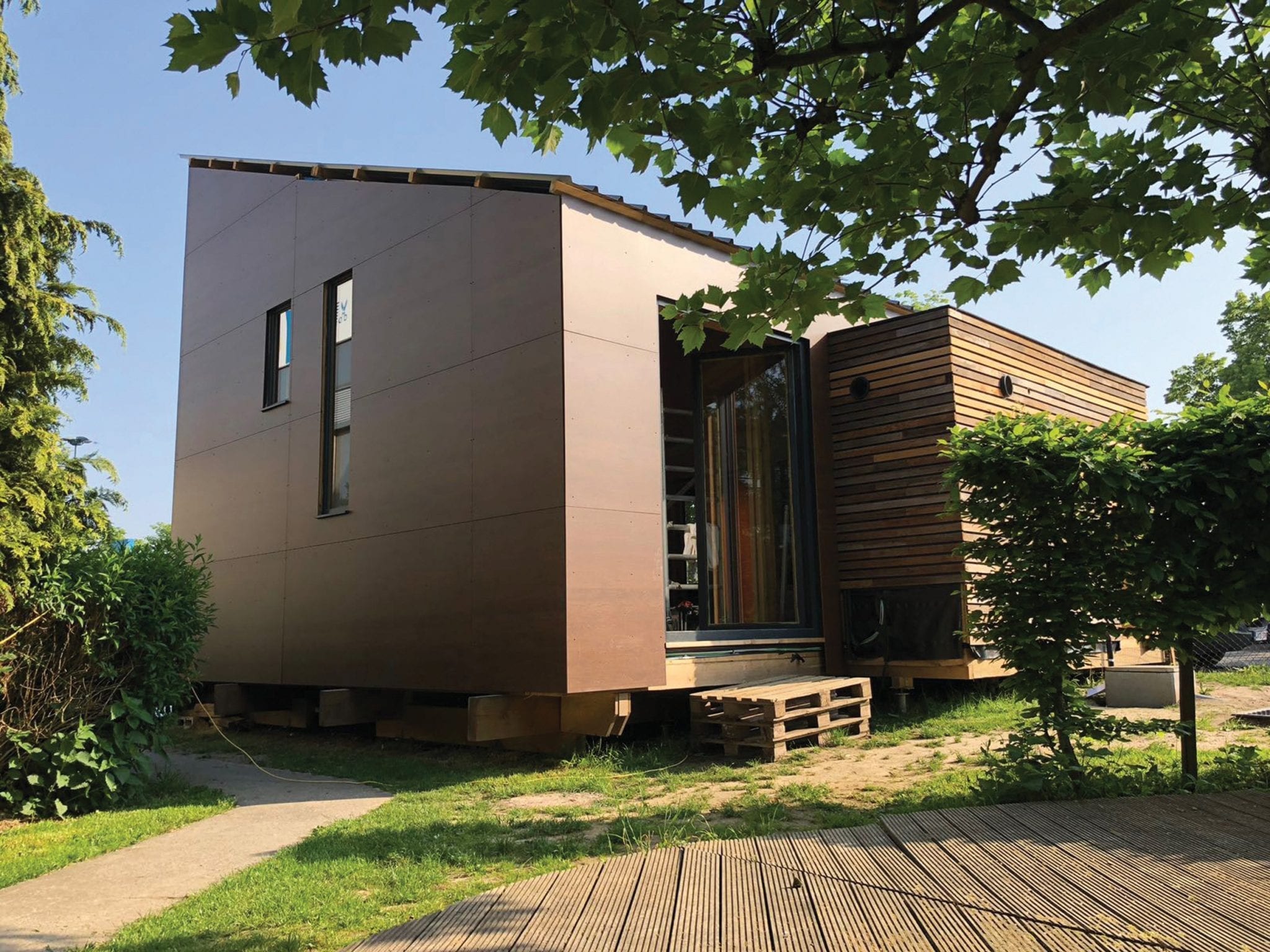
The Circular Retrofit (CRL)
CRL has 8 student modules on the university campus of the Vrije Universiteit Brussel in Etterbeek. Instead of demolishing the original 1960s buildings as planned, they were renovated. But it wasn’t just any renovation: the VUB Architectural Engineering research group tested new circular renovation solutions, together with industrial business partners. For the partitions and façades, for instance, they developed reversible solutions based on existing products.
In terms of costs, reversible construction turned out to involve a higher initial investment. This will however be recovered if you take into account the much longer life cycle of the building and the necessary transformations. In the long-run, reversible construction is therefore cost-efficient.
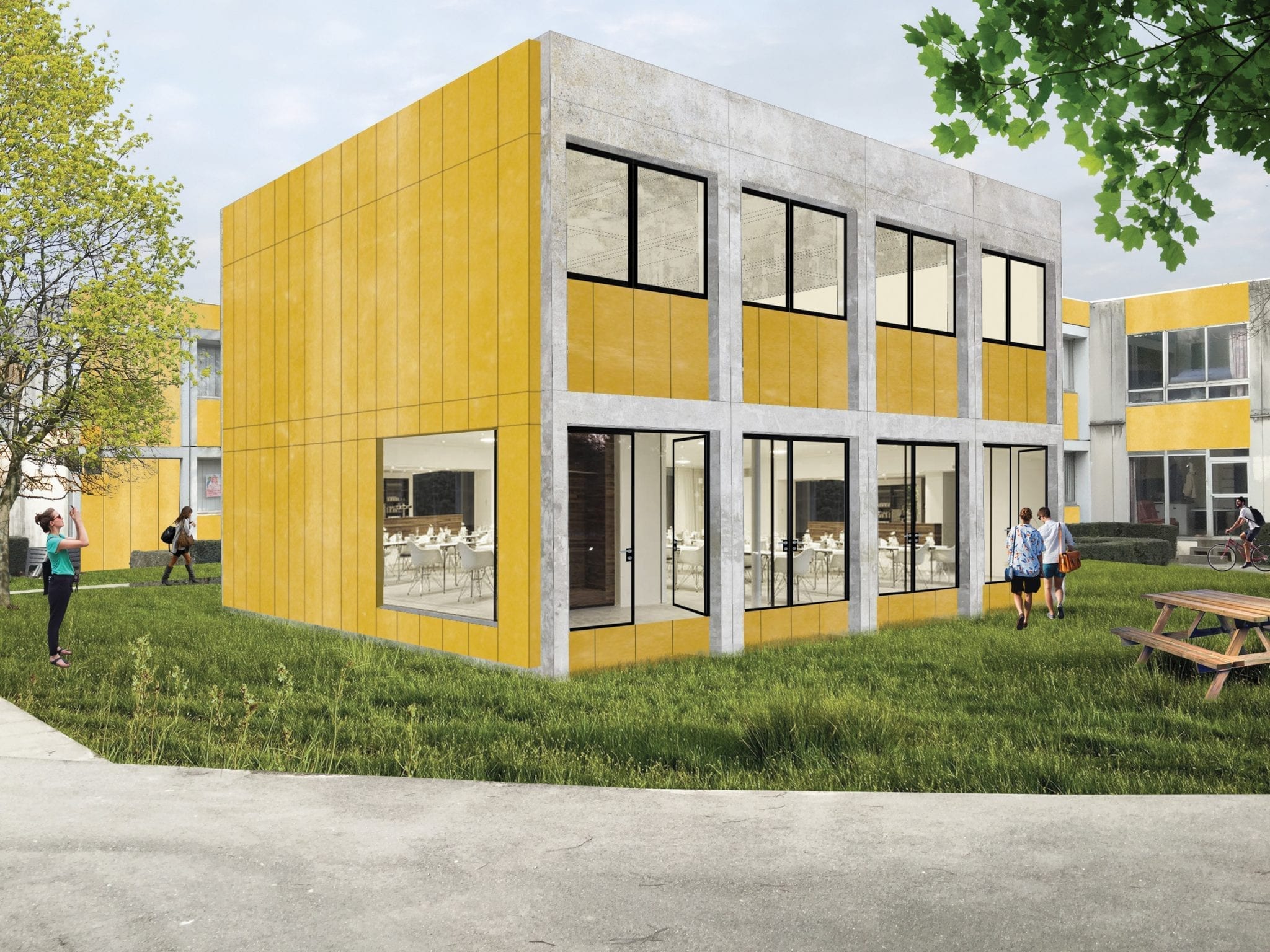
Tools for Professionals
What if construction professionals want to work differently? For them, the Region is developing several tools. The online Brussels’ Sustainable Building Guide provides tips for dismantling, reuse and recycling of construction materials. Information on Life Cycle Analysis (LCA) and the importance of choosing materials can be found in this guide.
In parallel, the Tool to Optimise the Total Environmental impact of Materials (TOTEM) 9 is a free online application – jointly developed by the three Belgian regions – launched at Batibouw in February 2018. TOTEM allows professionals to see the impact of their construction and renovation projects on the environment, and to choose the right materials and techniques to reduce that impact. The goal is to make TOTEM as user friendly and well-known as possible. Numerous events and meetings have been organized with users of the tool, including manufacturers of materials. To date, more than 1,400 people have used TOTEM and 240 architects have been trained.
These smart sustainability tools, together with the growing number of circular sites and buildings, prove that the new vision is taking a firm foothold in Brussels!