Unlocking Sustainable Fuels and Bio-Based Products
Making products and energy from renewable bio-resources (instead of from fossil fuels) is a key aspect to combat climate change, reduce our dependence on imported oil and stimulate economic growth in Europe. Producing cost-effective bio-butanol from sustainable feedstock is part of this transition.
The successful transition towards a more full-blown bioeconomy is dependent on the optimal use of biomass resources. Their availability is limited and the use of certain feedstocks, such as arable crops, raises concerns about their competition with food production and the greenhouse gas impacts of indirect land use change. Attention is turning to more sustainable feedstocks such as agricultural residues, biological waste and fast-growing energy crops, which do not compete with food production or contribute to deforestation. Transforming these sustainable feedstocks into high value products is technically challenging. Research and innovation is being undertaken to develop improved production processes that are cheaper, more efficient and environmentally friendly.
The Biobutanol Potential Prize
Fermentation is a conversion method that can be used to turn biomass into valuable products. Acetone–butanol–ethanol (ABE) fermentation uses bacteria to produce acetone, butanol, and ethanol from carbohydrates such as starch and glucose. The process may be likened to how yeast ferments sugars to produce ethanol for wine, beer, or fuel. Due to the rise of cheap petroleum-based production, ABE fermentation of biomass fell out of fashion in the second half of the 20th century, but driven by technological advances and the growing demand for sustainable alternatives to fossil fuels, this old process is now being rediscovered.
The main product of ABE fermentation is biobutanol. Biobutanol is considered an exciting alternative to first generation biofuels such as biodiesel and bioethanol. Interestingly, it is also a building block chemical used extensively in paints, coatings, adhesives and inks. Given this huge potential, funds are quickly being found for biobutanol production.
Currently, converting more sustainable woody biomass remains technically challenging. On top of this, each production step is frequently developed separately, leading to difficulties in optimization and scale-up speed. To overcome this, the EU-funded ButaNexT project set out to optimize the process at value chain level. During the 3 years of the project, ButaNexT developed and demonstrated, at pilot scale, a more cost-competitive, efficient and environmentally friendly process to convert sustainable renewable feedstocks into biobutanol.
Sustainable Feedstocks
First-generation biofuels are made from sugars and vegetable oils found in arable crops, which can be easily extracted using conventional technology. Second-generation biofuels are made from lignocellulosic biomass or woody crops, agricultural residues or waste, making it harder to extract the required fuel. The ButaNexT project focused exclusively on the latter, which are considered more sustainable.
4 Types of Sustainable Feedstock for Butanol Production
A feedstock assessment carried out by E4tech considered the availability across Europe of 4 types of feedstock that could be used for butanol production: straw, Miscanthus, the biological fraction of municipal solid waste, and woody biomass residues.
Straw
The wheat stalks left behind after harvesting are generally used as bedding for livestock or left on the agricultural fields to enrich the soil. A significant straw resource exists that can be sustainably extracted and used for alternative purposes such as biobutanol production. Potential EU availability: 58.4Mt
Miscanthus
Miscanthus (commonly known as Elephant Grass) resembles bamboo, grows over 3 meters tall, and produces a crop every year without the need for replanting. Its rapid growth and high biomass yield make it a promising feedstock for biofuels. Althought it is not currently grown widely in Europe, Miscanthus can be planted on unused or underutilised land to mitigate against indirect land use change impacts. Potential EU availability: 20.3Mt
Municipal Solid Waster (MSW)
Municipal Solid Waste (MSW) consists of all the everyday items that we use and throw away. This includes organic materials such as food waste that could be used as a feedstock for the biobutanol process. Potential EU availability: 150Mt
Woody Biomass Residues
Many different categories of woody biomass residues could be of interest as feedstocks for biobutanol, such as pruning residues (from vineyards), saw mill residues and saw dust, and primary forestry residues. Potential EU availability: 95Mt
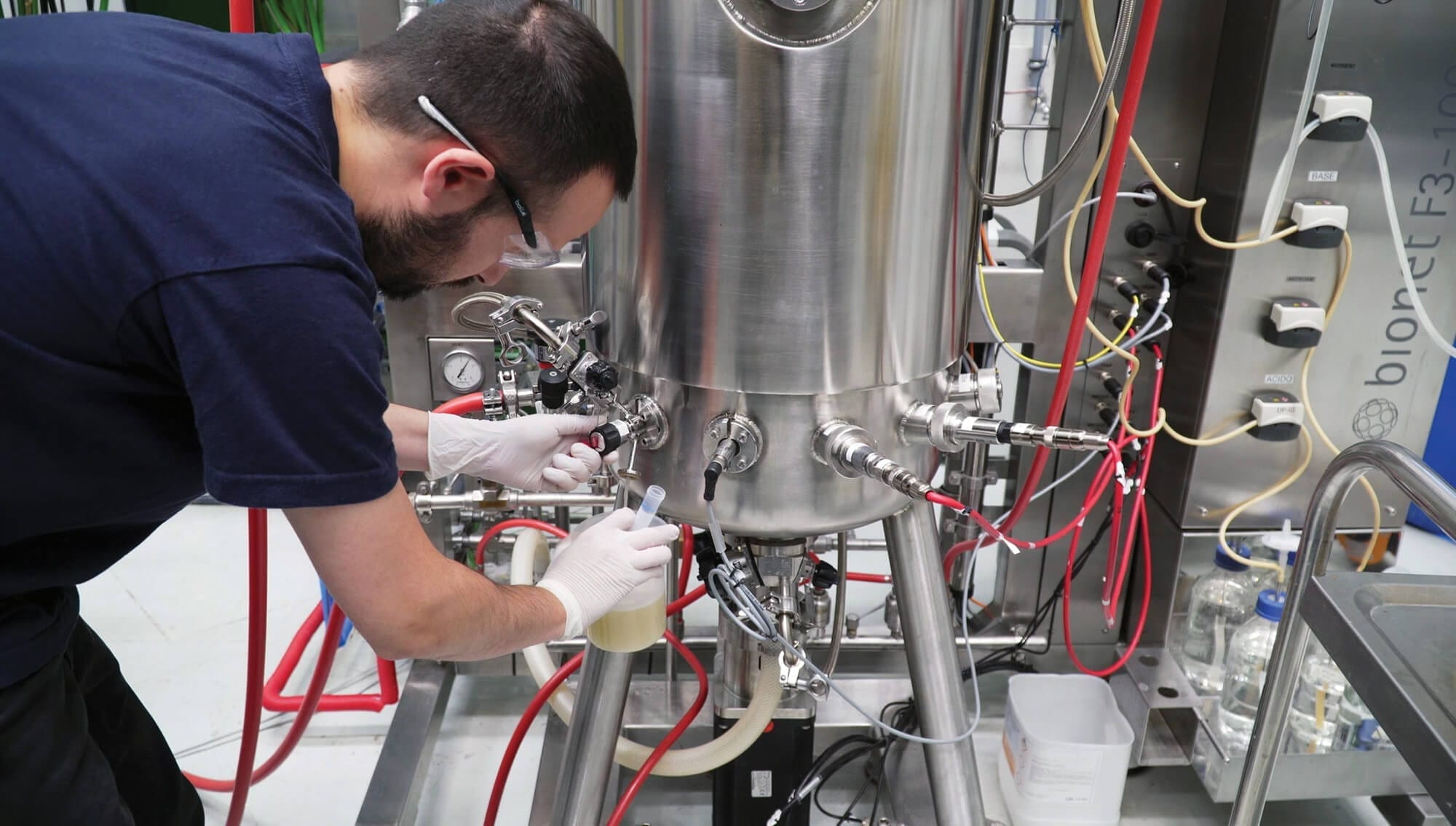
An Innovation Process in Action ButaNexT partners focused on 3 main productions steps:
1. Flexible Biomass Conversion: Tecnicas Reunidas, together with CENER, developed a new two-step pre-treatment process which converts different lignocellulosic biomass and wastes that provide higher yields in subsequent stages. Crucially, the new milling unit significantly reduces the biomass particle size (to less than half a millimetre). This allows for milder conditions in the subsequent thermochemical treatment, and an improved conversion rate during the hydrolysis stage. Both capital and operating costs can be reduced – the unit reduces the energy consumption up to 25% compared to the conventional technologies studied.
2. Tailor-Made Enzyme Cocktails: MetGen designed and developed tailormade enzyme solutions for non-food lignocellulosic feedstocks. The optimized cocktails increased total sugar yield by 70-90% compared to the initial offerings, in half of the hydrolysis time.
3. High Productivity Fermentation Process: Green Biologics developed an improved clostridial strain specifically for use with lignocellulosic feedstocks. The fermentation was coupled with membrane technology developed by the Flemish Institute for Technological Research (VITO) to achieve in situ product recovery (ISPR). This hybrid fermentation concept alleviates product inhibition and leads to partial product purification and enrichment, thus improving water balances and reducing energy consumption in further downstream processing.
The innovations were combined at a pilot plant, installed at the Second Generation Biofuels Centre operated by CENER – Spain’s National Renewable Energy Centre – in Navarra, Spain.
Environmental, Social and Economic Impact
It is one thing to make a process more efficient; it is another to translate this into actual social, economic and environmental benefits. In the ButaNexT project, an assessment of the impacts of producing biobutanol through the newly developed process was carried out by the company E4tech:
Environmental Impact | An assessment of a conceptual commercial-scale biobutanol plant showed that carbon emission savings of 22% can be achieved. This is encouraging, and large improvements are expected as the technology matures and further R&D is carried out. Specific improvements were identified that could have the biggest impact on reducing emissions.
Social Impact | The assessment examined the likely impact of a commercial-scale butanol plant. The results indicate that there are substantial job opportunities, particularly in the agriculture sector, from lignocellulosic biobutanol production.
Techno-Economic Assessment | Cash-flow modelling was used to estimate the financial viability of a commercial-scale biobutanol production plant using the ButaNexT innovations. All scenarios indicate there is a potential for the technology to be economically viable, with the main variables being how heat and power is provided to the plant, and the cost of feedstock and enzymes.
It is one thing to make a process more efficient; it is another to translate this into actual social, economic and environmental benefits.
Market Applications
Advanced Fuel
While no vehicles are approved by legislation to run on 100% biobutanol, there are blends of biobutanol with traditional fuels that can work with current engines. Researchers at University of Castilla la Mancha, also involved in ButaNexT, found that biobutanol as a blend component does not reduce engine efficiency and is beneficial for reducing particulate emissions (up to a maximum reduction of 60% in mass and 20% in particle number). Bio-Based Products Biobutanol can be used as a drop-in replacement for petroleum-based butanol in almost all applications. Its ability to be used as an additive has resulted in increasing demand from the pharmaceutical industry. The uptake of ButaNexT biobutanol by those industries could help them to be more sustainable in terms of their raw material use and allow them to position themselves within the green ‘bio-based’ market segment.
Advanced Processes
Most of the innovations and developments achieved in the ButaNexT project can be used for transforming lignocellulosic biomass into other biofuels and bio-based chemicals in general.
For generations the potential of bio-butanol has not been fully realized, but now the ButaNexT project has shown the path to how an advanced biofuel business can be built from sustainable feedstock. As followup to ButaNexT, learn more on pages 24-25 about the ongoing research and innovation of the EU-funded Horizon 2020 project called ADVANCEFUEL.