From Waste to Resource
Re-designing the value chain of water and minerals for industry
A new economy is emerging; one that is always keeping resources at the highest value and making use of all resources – known as circular economy. There is no waste, there is reuse – a concept that nature successfully applies for hundred thousands of years. The innovation project ZERO BRINE is advancing circular business models for process industries by redesigning the value chain of water and minerals.
Brine discharge, or complex saline-impaired effluents, are a major threat to the environment. Process industries are a major source of brine discharge, with the chemical industry alone producing 11.5 million tons of brine every year going along with high costs to manage. The good news is that brine is not just grey wastewater: industrial brine can contain many salts, chemicals, minerals, metals, other organics resulting and water from manufacturing and processing.
The innovation project ZERO BRINE funded by the European Union is developing a circular economy approach for the recovery of all resources from the brine generated by process industries – a disruptive method demonstrating a new way to deal with industrial wastewater. ZERO BRINE is redesigning the value and supply chain of water and minerals by recovering high-quality water, salts, minerals, metals, and even heat for use in the same factory or surrounding industries, thus closing the loop on the vast amounts of resources that are lost in current processing methods. At a time when EU is 100% import dependent on critical raw materials such as magnesium, the ZERO BRINE technology offers many benefits for harvesting second generation materials from wastewater. The ZERO BRINE solution contributes to the competitiveness of European industry whilst being in harmony with the environment.
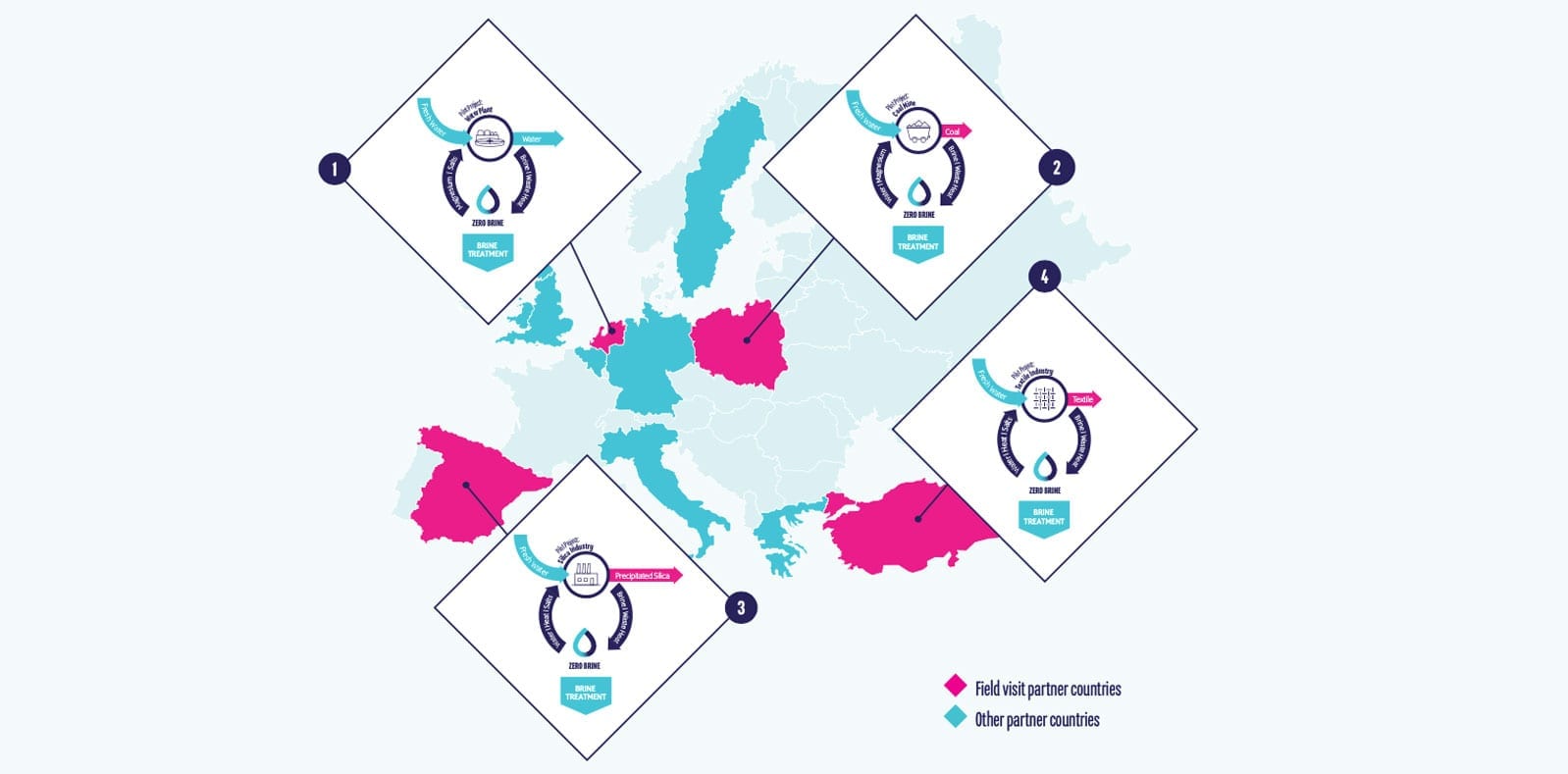
Replicating and scaling circular opportunities
ZERO BRINE technology can be replicated and adapted to wastewater from various industries demonstrated at the four demonstration plants across Europe: At the industrial cluster of Rotterdam Port in the Netherlands, the demineralized water supplier Evides Industriewater, at the silica factory IQE in Spain, in a coal mine in Poland operated by the Silesian University of Technology and in a textile factory in Turkey at ZORLU Textile Energy Group. These large-scale demonstration plants provide the potential for immediate replication and uptake of the project results after their successful completion.
Industrial symbiosis will play a key role in cutting down costs but also environmental impacts through waste heat recovery. To facilitate market uptake, ZERO BRINE developed an Online Brine Platform, a web platform to connect industry, technology providers and end users. This digital platform will advance the industrial cooperation in Europe and worldwide, provide effective brine treatment solutions to process industries and ensure extensive knowledge exchange and dialogue between key stakeholders. In addition, five Brine Excellence Centers integrated in partner organizations in the Netherlands, Italy, Greece, Poland and Spain will provide the opportunity for end-users to test and develop customized and validated brine treatment solutions.
ZERO BRINE is a good practice for circularity in Europe that can increase efficiency and productivity, decrease costs and create jobs in harmony with the environment. With innovative technology, business cases, supportive policy and a mindset for collaboration the circular economy has good potential to become the new mainstream.
Interested in brine stream valorization? Join European frontrunners seeking circular business opportunities!
The Online Brine Portal brings together content from various sources in a single web page and facilitates the use of the Online Brine Platform.
The portal enables consultation and consensus building with the relevant stakeholders, facilitating the exchange of information and data produced by ZERO BRINE project.
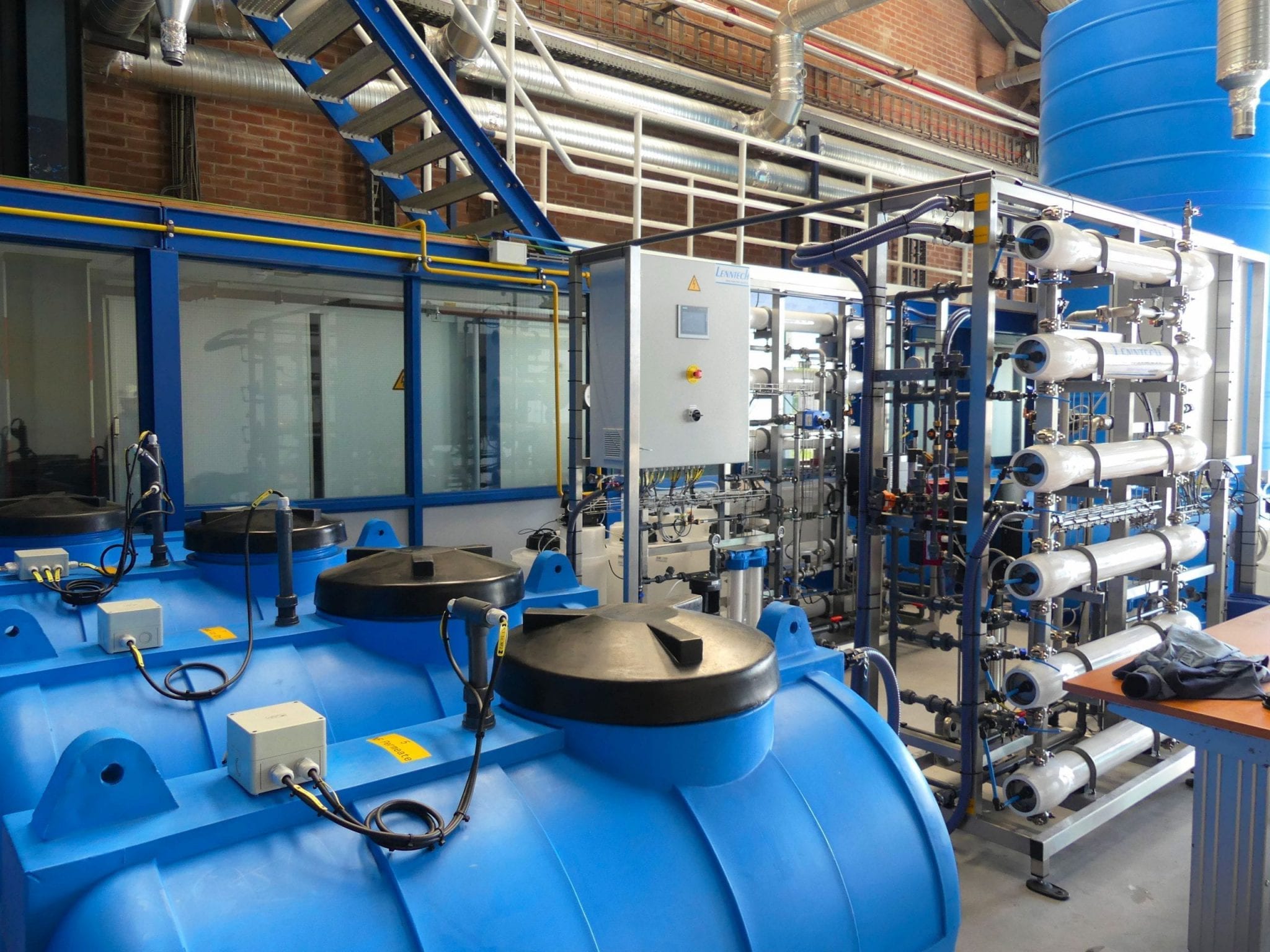
Demineralized Water Plant, Evides (ROTTERDAM, NETHERLANDS)
At the Demi Water Plant (DWP) of Evides in the Botlek industrial area, ZERO BRINE demonstrates the circular economy approach to treat industrial wastewater through redesigning the current brine treatment process from a linear to a circular model recovering all the resources. A large-scale demonstration plant is tested at PlantOne, a test facility focused on sustainable technology and innovation in the Energy Port and Petrochemical cluster of Rotterdam Port, by using the waste heat from one of the factories in the port. The objective is to recover Ca- and Mg-salts as well as demineralized water from the discharges of the water-softening unit. The quality of the recovered products will be aimed to meet local market specifications.
Business opportunities
Industrial saline impaired effluents (brines) are an environmental challenge and an economic opportunity. The following materials with potential commercial value are recovered on the two sites that will be used in the same factory by Evides or in the industrial area Botlek:
- High purity magnesium & calcium
- Clean Water
- NaCl regeneration solution
- Sulphate salts
- NaHCO3
- Clean Water
- NaCl regeneration solution
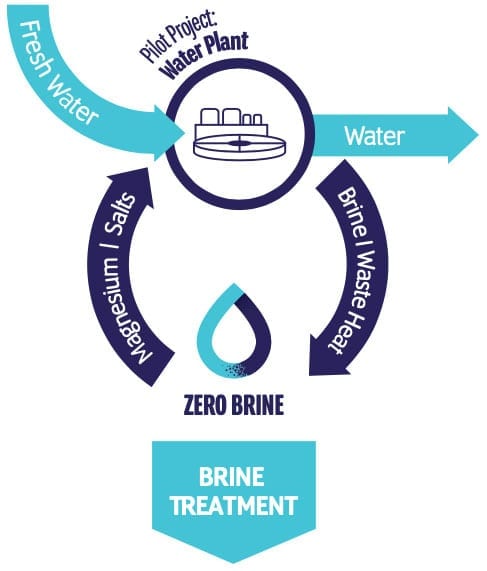
Coal Mine Bolesław Śmiały, Silesian University of Technology (ŁAZISKA GÓRNE, POLAND)
Saline wastewaters are a concern of many industries. The coal mining industry is particularly affected: every year Poland discharges around four million tons of sodium chloride (salt) into rivers, coming mainly from coal mines. This causes environmental damage and economic strains due to pollution fees. ZERO BRINE aims at providing a technological solution of the saline wastewater problem for the coal mining industry. The ZERO BRINE technology is expected to decrease the energy consumption in the production of concentrated brine by 50% (target: 22 kWh/m3 of brine treated), compared to the vapour compression technology already used in Czerwionka-Leszczyny. The technology will also allow the recovery of raw materials: evaporated salt or concentrated brine, which both have multiple applications in the chemical industry, as well as magnesium hydroxide, which is a valuable commodity in the refractory materials industry.
Business opportunities
The problem of saline wastewaters is not unique to only one mine or one company – it has been a systemic issue throughout the whole industry for years. At the moment, 18 hard coal mines are still operational in Poland and might be interested in turning their big environmental problem into a potential source of income. An important business opportunity is the production of salt. The average production in Poland is around 4.3Mt/y, with salt-in-brine accounting for around two-thirds of production. Some 63% of salt-in-brine produced domestically is consumed in two synthetic soda ash plants (operated by Soda Polska Ciech). Around 21% of salt-in-brine is used in the production of evaporated salt and 16% in chlor-alkali production (by Anwil Nitrogen Plant, PCC Rokita and Organika-Zachem Chemical Works). The magnesium hydroxide is of interest for the refractory materials industry. In 2006, the production of refractories in Poland reached nearly 300,000 tons, around 28% of which were unshaped materials. The main manufacturers in Poland include ZM Ropczyce S.A., PMO Komex (part of Alcerol-Mittal), PCO Z ̇arów S.A., Vesuvius Skawina.

Silica factory, IQE (ZARAGOZA, SPAIN)
Silica industry produces between 21 to 46 m3 of saline wastewater per ton of silica containing between 13 and 28 mg/L of sodium sulphate and is normally discharged to natural watercourses (rivers, sea) after passing through wastewater treatment plants; a cost-intensive process. The silica industry consumes up to 40m3 water per ton of silica. During drought periods, guaranteeing water supply is a challenge. Difficulties in brine management can hinder a company to increase production. Water recovery enabled by the ZERO BRINE technology aims to ensure water supply and reducing costs associated to the water consumption. Nanofiltration and crystallization pilot plants will be 5 implemented at IQE in order to demonstrate and test these technologies for resource recovery from wastewater. Additionally, heat waste recovery strategies will be evaluated.
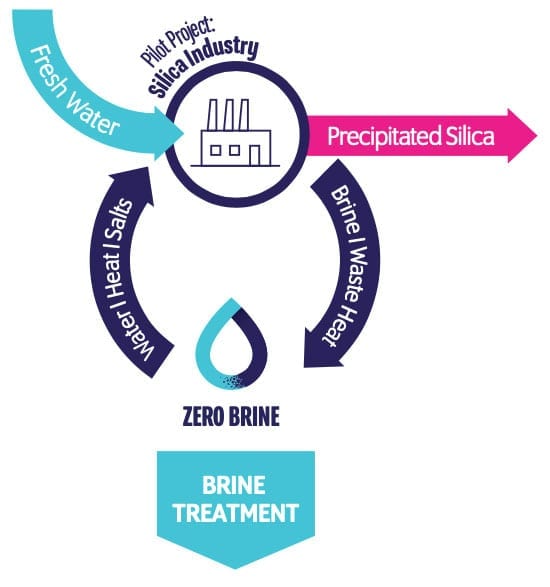
Business opportunities
The proposed solution will allow up to 70% of quality water recovery that can be reused in the silica production process, thus reducing overall water consumption in the company as well as 0.75 tons of anhydrous sodium sulphate per tonne of silica produced. ZERO BRINE improves the efficient use of resources and reduces the environmental impact of the silica process both enhancing the profitability of silica production.
Textile factory, ZORLU Textile – Energy Group (BÜYÜKKARIŞTIRAN- LÜLEBURGAZ, KIRKLARELI, TURKEY)
An innovative brine treatment system is being developed for the textile industry with the aim to recover concentrated salt solutions for reuse in the textile dyeing process baths by TUBITAK MRC in cooperation with ZORLU Textile and Energy Groups at Büyükkarıştıran- Lüleburgaz, Kırklareli, Turkey. The methodology involves initial comprehensive physical, chemical characterization studies which are followed by bench scale treatability studies with technology options tested such as nano filtration, oxidation and ion exchange.
Expected Achievements
The developed process scheme will result in 70-75% recovery of salt for dyeing processes or for other purposes within the enterprise. Treated water, permeate of Reverse Osmosis treatment unit alternatively will be reused within the enterprise for various purposes. Additionally, the evaluation of the environmental benefits, social benefits and the economic feasibility of the innovative ZERO BRINE textile demo case is appraised. The overall expected results from textile industry brine recovery system is estimated to be 50 kt/year reduction water consumption due to achievement of additional water reuse, recovery of 400 tons NaCl/year for production processes, reduction of 200 t/year CO2 emissions also due to NaCl recovery.
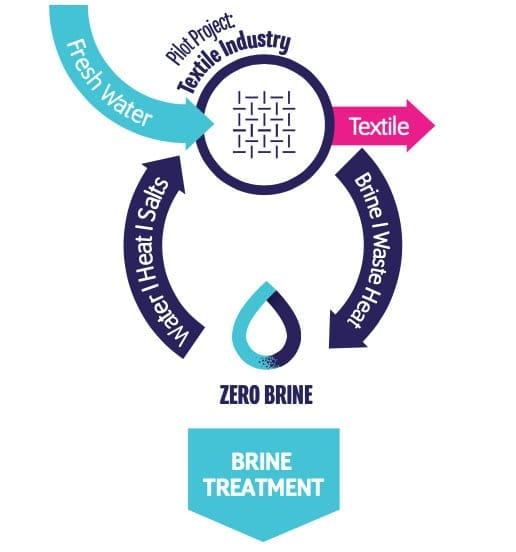
ZERO BRINE
Coordinated by TU DELFT, the innovation project ZERO BRINE advances circular economy business model solutions to reduce industrial saline wastewater streams by recovering and reusing the minerals and water from the brine in other industries. Four demonstration projects in the Netherlands, Spain, Poland and Turkey demonstrate innovative technologies to recover water and minerals of sufficient purity and quality for good market value, thus ‘closing the loop’ and improving the environmental impacts of production. ZERO BRINE is funded by the European Union’s H2020 Research and Innovation Program and includes 22 partners from research institutes, SMEs, construction companies, and end-users from 10 countries across Europe.