Designing the Wind Turbine of the Future
Quiet. Durable. Efficient.
Technology innovations that enhance turbines and reduce costs are needed to propel the wind sector and maintain Europe’s technological leadership. A group of key industrial players and research centers have joined forces to demonstrate their innovative designs on a working turbine in Spain.
Winds of change
The wind industry has changed beyond recognition in the last 30 years. Onshore, 20 meter turbines with a capacity of 50kW have given way to 2MW models stretching over 100 meters into the sky. Offshore generation only began in 1991. Since then more than 3000 turbines have been installed in
Europe’s waters, together providing more than 11,000MW of installed power.
The industry will continue to evolve in the future. Offshore wind is expanding at pace and developers will explore deeper waters further out to sea in search of new sites with stronger winds. On land, due to the gradually diminishing availability of sites in Europe farms will be located in lower wind areas and possibly closer to urban centres.
The consortium focused on enhancing three key components with high improvement potential – the blades, power electronics and the controller.
These changes create new challenges for the sector. The difficulty with repairing and maintaining deep-water offshore turbines makes reliability a growing priority for manufacturers. Onshore turbines will need to strive for the highest levels of efficiency and performance to maximise the energy extraction from lower winds. They must also be quieter to minimise noise pollution.
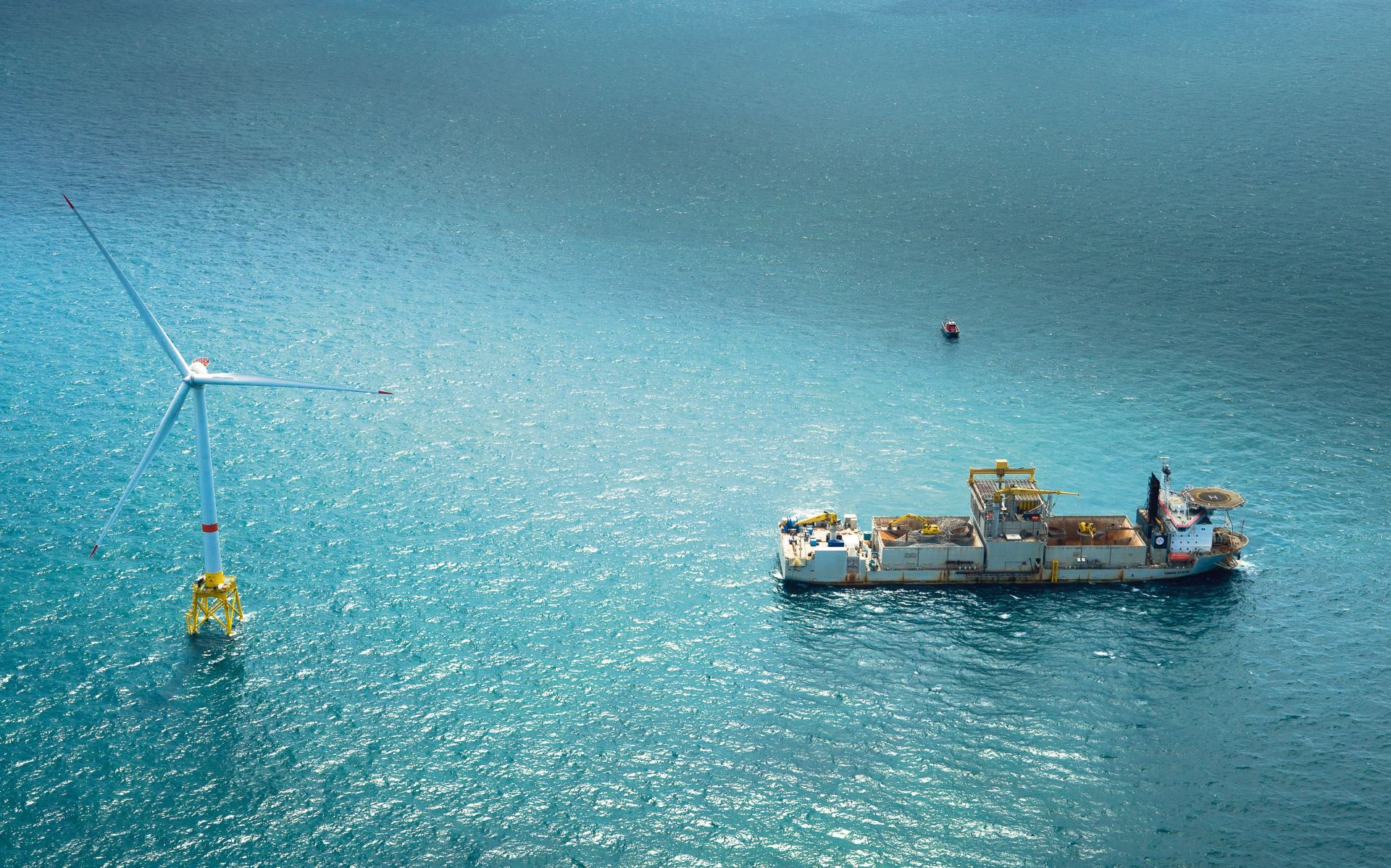
Reducing the cost of wind energy
Improved reliability and efficiency will also contribute to a lower cost of wind power. For the wind industry, as with all energy sources, reducing the cost of the generation process is the key to greater competitiveness. The cost of electricity from wind power has already experienced a stunning drop, falling by about two thirds between 1988 and 2014. As a result, the price of electricity from farms in high resource areas can now compete with more traditional energy sources. However, to achieve widespread grid parity, and boost Europe’s global competitiveness, further cost reductions are needed.
Reliability and durability have a profound impact on a project’s operation and maintenance (O&M) costs. Reducing the need to replace parts and extending the periods between scheduled maintenance reduces running costs. Improved turbine efficiency also boosts overall performance, optimising the balance between energy production and machine life.
Future cost reductions in wind energy will largely hinge on driving down operation and maintenance (O&M) costs, which currently account for between 20-25% of the LCOE of an onshore wind project.
O&M costs represent the second largest cost after upfront capital costs (turbine manufacturing, construction, planning and grid connection), accounting for around 20-25% of the total Levelized Cost Of Electricity from a given project. There is therefore significant scope for cost reductions in this area.
Technology innovations must arise to realise these cost savings. During the last three years, prominent industrial players and research centers in Europe have been working in collaboration on this very issue. The ‘Windtrust’ consortium have combined forces to devise an enhanced, next generation turbine. By optimising the design, operation and maintenance phases the group have extended the limits of reliability and availability, as well as reducing overall costs. The consortium focused on enhancing three key components with high improvement potential – the blades, power electronics and the controller.
1. Improved Rotor Blades
Rotor blades are put under a lot of strain. Completing up to 20 rotations a minute the blade tips can reach speeds of 180 miles per hour generating a huge amount of force. Factor in rain, hail and other particle impacts and it is hardly surprising that the blade surface can be susceptible to erosion. The problem is particularly acute for offshore turbines, which are typically larger – increasing tip speed – and exposed to salt water.
Leading edge erosion has multiple knock-on effects. Naturally it shortens the lifetime of the blade and results in increased O&M costs, but also leads to a significant loss in annual energy production, caused by the extra downtime and reduced general performance. The LCOE increases as a consequence.
Manufacturers are constantly looking to optimise blade designs in order to extend their lifetime. The blades, which are produced in huge specially designed moulds, must be strong and light, but also cost effective. They are made from composite materials such as fibreglass, reinforced polyester or wood-epoxy. Within the framework of Windtrust, Spanish company Gamesa has continued to explore the use of carbon fibre in rotorblades. Carbon fibre is renowned for its stiffness and extreme lightness, and the increased durability and reduced weight will extend the overall life of the turbine up towards 30 years.
The use of carbon fibre to increase durability and reduce weight will contribute to extending the overall life of the turbine to 20-30 years.
Alternative solutions to protect the blade surface against erosion have been developed in the past. Systems which apply tape or a gel coating to the blade edge have been used but lack durability, suffering from a high repair frequency.
In the search for a better solution, a new leading edge protector called ProBlade has been developed by LM Wind in Denmark. The unique system comprises an innovative Polyurethane brush-on coating that is applied to the blade, which has proved to be much more durable. The ProBlade has been trialled in extreme environments, undergoing state of the art accelerated rain erosion testing. The tests show huge improvements compared to previous systems, with the ProBlade performing five times better than tape, and more than 50 times better than the gel coat. These positive results represent the first step towards widespread adoption.
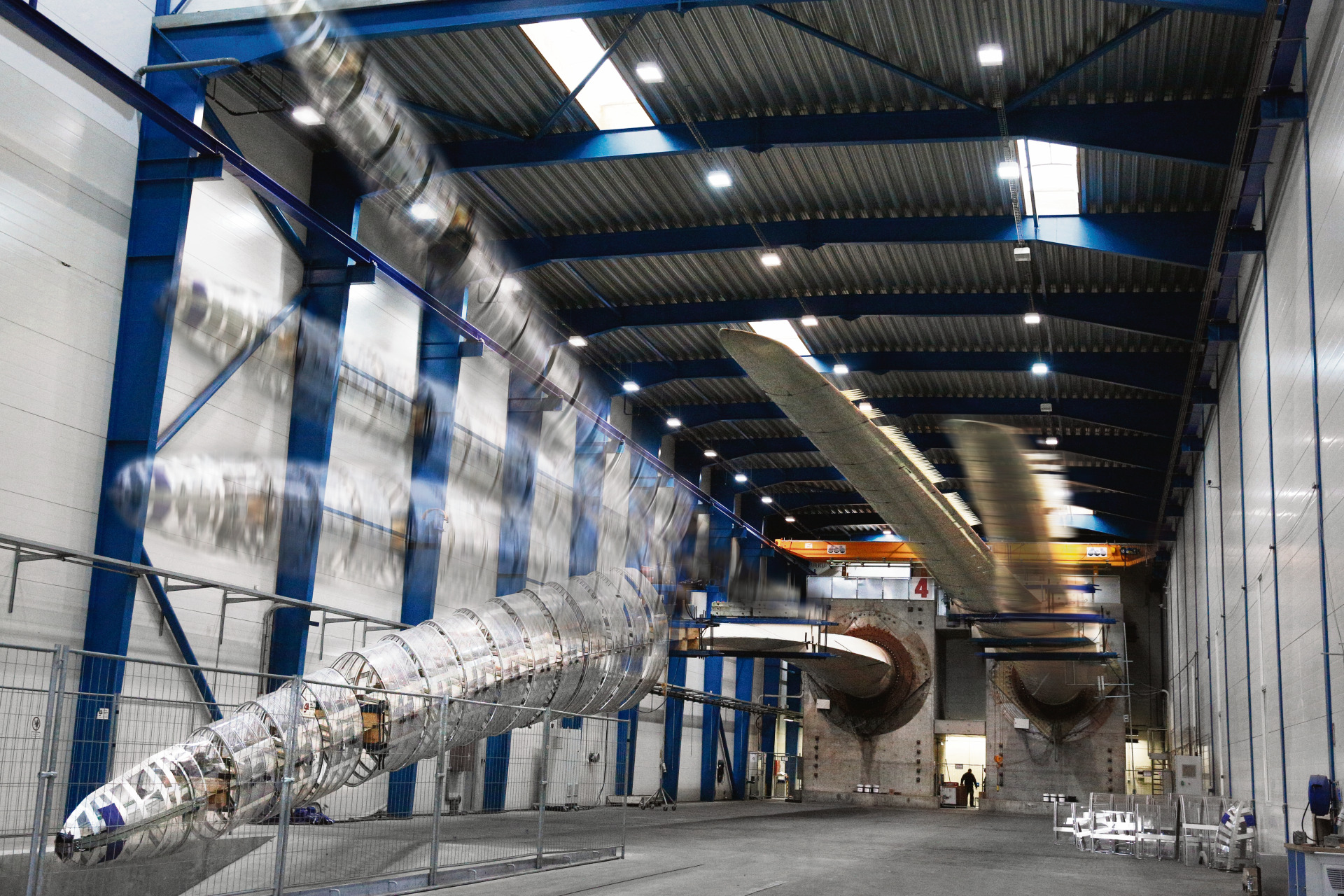
2. Optimised Power Electronics
The voltage and frequency of electricity generated by turbines must be adapted before it can be transferred and used. This vital task is carried out by the power electronics, which convert the non-regulated power from the generator into an AC output voltage of 690 volts, changing the basic characteristic of the wind turbine from being an energy source to an active power source. The converter has a generator and a line inverter to feed a voltage waveform into the electricity grid. Due
to its crucial role in the generation process, increasing the reliability of the power electronics is critical to the turbine’s annual energy production.
In order to achieve the highest possible level of reliability, German firm Semikron has been looking to optimise the design of its power electronics component by focusing on three aspects – humidity protection, scalability and reducing the number of parts.
Usually located in the nacelle, the power electronics are often exposed to vibration, humidity and dust. Semikron has improved the sealing and heating systems, particularly to reduce humidity levels – any condensation that occurs can result in water flows with catastrophic consequences. As turbines increase in size, power electronics modules have to be combined in order to convert power of 6MW or even more. Semikron has therefore sought solutions to make the component more compact, with its new intelligent power module having a 30% higher power density than previous models. Having successfully reduced both volume and weight, this will help limit the weight of the nacelle.
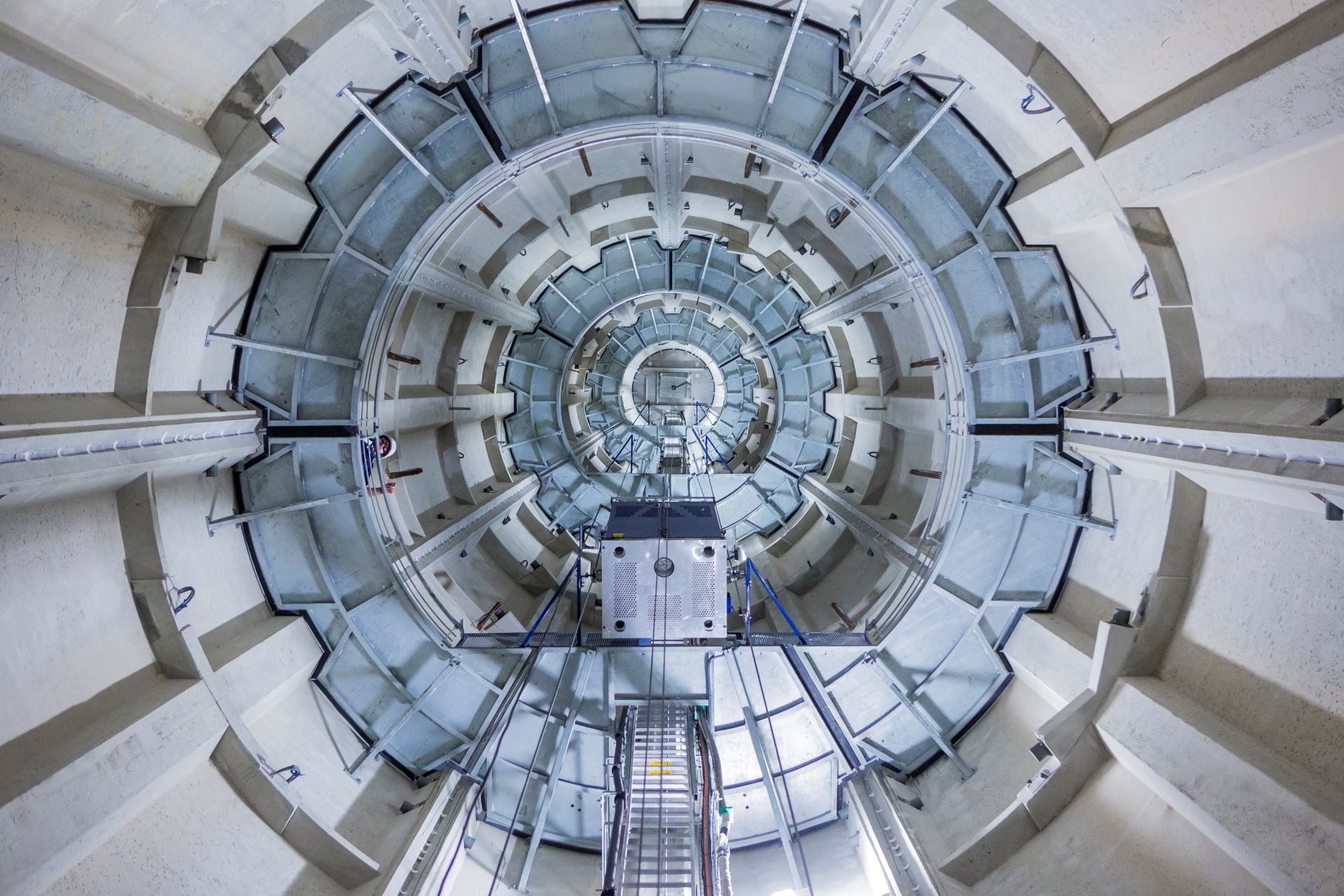
Statistics show that more parts equals more failures. By revising their entire assembly technology, Semikron’s new power module has been produced with 50% less parts compared to other examples on the market. The more compact component has the added benefit of helping to reduce system costs – smaller components mean that racks, connectors and cables are all reduced. This newly optimised design has gone through rigorous testing which has shown a significant improvement in both reliability and durability.
The need for compact systems, with high reliability and low cost, means that new technological approaches are demanded and the traditional modules used in power electronics will gradually vanish from the market.
3. Smarter Wind Turbine Controller
Though a large amount of research is undertaken to identify the best locations for wind farms, wind speed and direction remain hard to predict. To combat this, certain control methods are used to manoeuvre the turbine in order to maximise the energy generation at any given time.
The most common control variables are adjusting the ‘pitch’ and the ‘yaw’. Pitch control is specific to the blades and their ‘angle of attack’ with respect to the incoming wind, while yaw refers to the horizontal rotation of the entire wind turbine.
Apart from the inherent difficulty in identifying the most optimal turbine position, inaccuracies in turbine design and instalment are also a challenge for the controller. The enormous size of the turbines makes millimetre-precise installation virtually impossible. The resulting discrepancies between the paper plans and the installed turbine mean that monitoring is extremely complicated.
Enhanced turbine control algorithms will optimise the balance between energy production and machine life.
As well as finding ways to overcome these positioning errors, Gamesa has been developing control algorithms to enhance the pitch and yaw controller. The two control methods are used to either optimise or limit power output. At low wind speeds the controller seeks to optimise, to run the turbine at maximum efficiency and extract all available power. When winds are stronger than ideal, the controller looks to limit the generated power.
The enhancement of the smart controller will significantly increase the performance and energy production of a turbine – misalignments of just 5 degrees can cause thousands of euros of energy loss per year. The algorithms will also help reduce extreme and fatigue loads which threaten the structural health of the turbine. This will reduce maintenance costs by preventing breakdowns, and extend the overall lifetime of the turbine.
A better deal
Greece’s Centre for Renewable Energy Sources and Saving (CRES), were one of the organisations responsible for testing the enhanced components, with Levelized Cost of Electricity being a key indicator. Andreas Makis, research engineer at CRES is excited about the results, “the total reduction of the LCOE could theoretically range between 14-22%” he explained “and the innovations would have an even larger effect on wind turbines of larger capacity, and on offshore developments.”
The total reduction in costs could range between 14 and 22%.
Cheaper electricity production guarantees a better deal for consumers and a higher likely return for investors, improving the business case for wind power projects. The technology innovations developed by Windtrust will help the sector to keep growing, as it aims to serve a quarter of the EU’s electricity needs by 2030.
Q&A: Jesper Madsen
As wind energy expands, future wind turbines will be built closer to urban areas, making noise levels increasingly important. Jasper Madsen is chief engineer at LM Wind Power who have been developing innovative noise-reduction solutions.
What factors influence turbine noise?
“What most affects the noise level is actually the speed of the blade tips and the rotor diameter. Blade lengths have been growing considerably during the past years, as wind farms have been installed in lower wind speed sites, thus increasing the swept area to increase energy generation.”
How can turbine noise be reduced?
“One of the ways to deal with noise issues today is to stop the wind turbine in certain wind directions, or run the turbine in low-noise mode. However, both actions have a negative impact on the energy generation.”
What solutions has the Windtrust project advanced?
“Some of the latest developments in this field are serrations – serrated plastic panels mounted on the trailing edge of the blade. These serrations act as flow control devices, which focus on lowering the noise emission from the blades. Their lightweight design and simple mounting process make them an
attractive choice not only for new turbines, but for those already installed. By bringing the noise under the authorised limit more machines can
be installed. And crucially, at wind farms in noise-restricted areas, turbines equipped with this technology will be able to run at an optimal setting and therefore have a higher annual energy generation.”
Q&A: Fernando García Ayerra
Chief Engineer Technology Development at Gamesa and Technical coordinator of WINDTRUST discusses the impact of the project, and the future of wind energy in Europe.
How have you validated the results of Windtrust?
“The innovative components have been fitted onto an onshore 2 MW prototype turbine located at the experimental Alaiz Windfarm in Pamplona, Spain. This will enable us to compare the performance with those of existing, well-known turbines. Although this project is primarily aimed at onshore, most of the results are also applicable to offshore, where much greater benefits should be obtained.”
What is the expected impact of these improvements?
“Although the cost of the enhanced parts will probably be higher, the reduced cost of repairs and less downtime will render an increase in the amount of energy produced. This increase is expected to exceed any additional costs, thereby leading to an overall reduction of the cost of energy. It is important that people understand that all the money invested in R&D is focused towards the reduction of the cost of wind energy, which will hopefully reach the final consumer.”
What does the future hold for wind energy generation across Europe?
“In Europe we want to achieve a clean reliable energy supply at the lowest possible cost. The creation of a truly European energy market and system, that is, pricing, transport and management, will allow the maximum deployment of sustainable energy generation sources.”