The Value of Building with Mud
A return to traditional construction methods offers a number of benefits, especially when it comes from the earth.
Mud versus cement is a modern-day debate in India, where age-old traditionally sustainable materials and methods of construction have been replaced by cement in the name of growth and efficiency. As a diverse country with numerous cultures and beliefs, India is home to many construction techniques as well. Most of them use local materials, some of which have lasted centuries. However, these methods seem to be slowly giving way to more modern techniques that are not always suitable across the varying landscape of the country. Traditional construction techniques are being lost to strong and easy-touse cement, which has found its way into the construction industry over the last century and seems to be here to stay.
Cement is being used in every corner of the country without consideration for the surrounding temperature or climatic conditions. Southern India is an amalgamation of hot, humid, dry and cold temperatures. The west coast experiences more than five months of heavy monsoons, while the east coast is often submerged in just one month of monsoon. The coastal regions are humid while the interior is dry and hot. In between, we have small mountains and hills with a cool climate throughout the year. In northern India, we have the Himalayas on the eastern end and the Thar Desert to the western. Considering this, one material like cement should not be used for construction in all these climates. The traditional methods used in these areas should be respected and revived.
Adapting to the climate
Traditionally, laterite stone was available in abundance on the western coast of southern India, and was usable for strong, porous walls of a reddish hue, plastered with a mixture of clay and lime, which enabled breathability throughout. During heavy rains, the sloping, clay-tiled roofs ensured water did not stay stagnant or seep into the walls, while also making repairs easy. This technique was effective in adapting to the climatic conditions while generating very little construction waste. Everything was biodegradable or reusable.
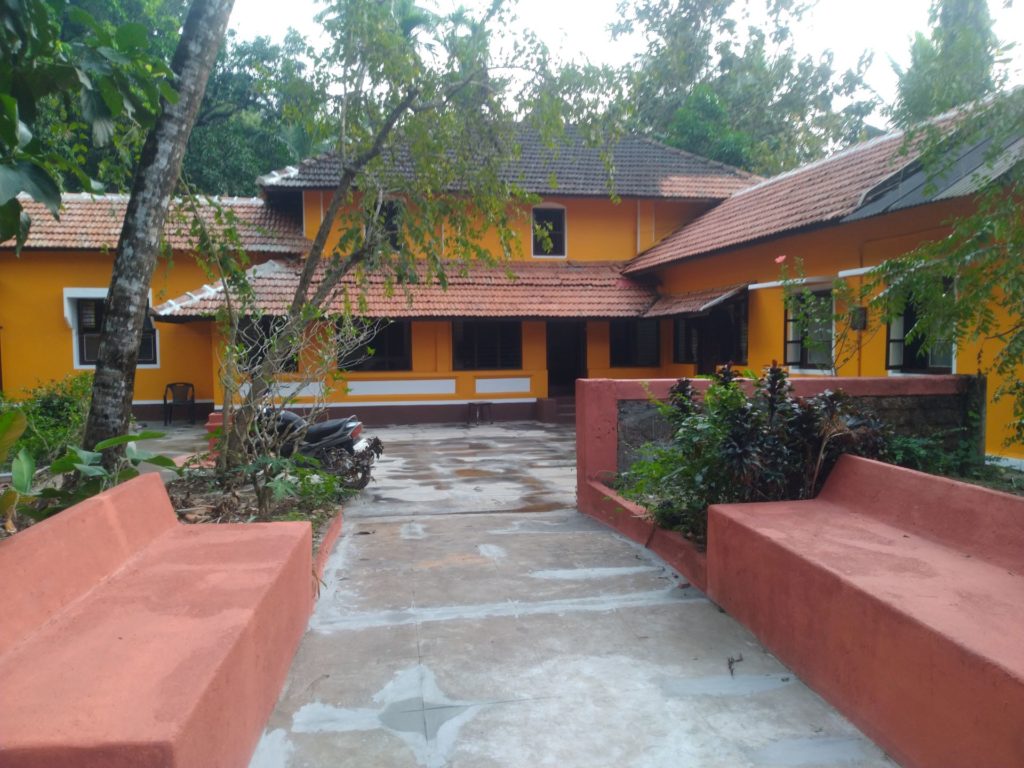
But now, clay tiles and mud and stone walls are considered weak. The mud-plastered traditional houses are considered kuccha (raw or weak) houses, and the newer cement-plastered houses are considered pucca (strong) houses. This differentiation was even taught in schools, ensuring that children understood the importance of growing up and building a strong cement house. This plays a major part in changing the mindset of most Indians. People who owned traditional houses which were more than 50 or 100 years old would save up and raze the old ‘kuccha house’ for a strong, modern cement one.
Plastering with natural materials is effective in adapting to climate conditions while generating very little construction waste: everything is biodegradable or reusable.
Soon, all the laterite walls were plastered with cement, stripping them of their porosity and breathability. Over the last decade, the laterite stone walls were replaced by fire brick walls, which led to more pollution as the kilns manufacturing these bricks are considered one of the most polluting plants in the construction industry. Sloping roofs gave way to flat reinforced cement concrete (RCC) roofs, which are stronger and cannot be damaged by falling coconuts or monkeys.
During heavy monsoons, water does not drain off the flat roofs as easily, and most houses now have seepage problems. In summer, RCC roofs absorb heat, making the flat-roofed houses unbearably hot. As a result, people have started putting a sloping galvanized iron sheet roof over their flat terraces to ensure water flows down in the rainy season, and there is no direct heat on the roof in summer. Some households use these iron sheets directly to avoid problems caused by flat roofs, but these sheets also absorb heat and create an unbearable environment inside the house.
The Himalayan Belt of North India
In the higher Himalayas, characterized by cold snowy weather and heavy monsoon, locallyavailable slate stone and wood were used in traditional methods of construction to create breathable and easily replaceable sloping roofs. Walls were made with dry stone masonry and then plastered with local clay. This ensured proper thermal insulation, so the houses remained warm in the cold winters, especially when a fire was lit inside the house. Wide, decorative windows and doors ensured sunlight reached every nook of the house and allowed people to interact with their neighbors.

However, by 2023, cement found its way even into some of the remotest villages. People carry heavy sacks of cement on their backs, on pick-up trucks or mules, and proudly build cement houses. Come winter, most of them head to the kitchen – the one room which usually still has mud plaster – to sleep, as cement walls in the rest of the house retain little to no heat.
My mud home in the Himalayas
To demonstrate the benefits of traditional buildings, in 2022, I built my own mud home in the remote Himalayan village of Wan, in the state of Uttarakhand. Wan is a beautiful village located at an altitude of 8,000 feet above sea-level and is the last village accessible by road in that region. Beyond Wan, the mighty Himalayas take over.
To build the foundation, I used the traditional dry stone masonry technique where stone pieces are laid one on top of the other without the use of cement or mud plaster. For the walls, I used a method called ‘earthbag’ or ‘super adobe’ construction. Here, we reuse empty discarded sacks of cement, fill them with the mud, stone or soil available on-site (I used soil and stones that had fallen from landslides across the village), and build thick, strong walls. As the layers of sacks went up, villagers passing by stopped to see, both out of curiosity and some skepticism regarding the durability of such a construction.
The village children would help me make the mud plaster in the morning before they left for school, after which I would apply the plaster for the rest of the day. Even the adults joined in.
When the walls reached the required height, it was time for me to start plastering them with mud. Typically, water and clay are used as a plaster coat, but such a plaster would crack easily when stuck to the plastic sacks. Instead, I used cob, a mixture of clay, straw and the local soil (in this case, black soil) in a specific proportion which ensures the plaster sticks to the wall. Unlike simple clay plaster, cob, due to the stickiness of the clay, the fineness of the soil and the binding property of small pieces of straw, is held together and sticks firmly on the wall.
The process of making cob is similar to traditional wine-making in that we mix the materials with our feet. Everyone wanted to jump in and mix the cob, an activity that took a couple of weeks. The village children would help me make the mud plaster in the morning before they left for school, after which I would apply the plaster for the rest of the day. Even the adults joined in too.
Soon, the walls were plastered, the roof was up and the villagers who used to pass by started stepping in to see the house. Everyone was amazed. One local man asked me if he could rent it for the winter because it was so warm and cozy inside. These are the advantages of the traditional methods that have been replaced by modern cement houses. I am glad that because of my attempt to build a small cottage, one remote village in the Himalayas now knows the advantages of these traditional methods.

A return to traditional building
People are slowly realizing the disadvantages of cement after more than three decades of it being a part of almost every house in India. While traditional houses have lasted 70 to 100 years, the new cement houses last 30 to 40 years, and most of them develop seepages and cracks.
After the lifecycle of a house is completed, the construction waste of cement houses ends up in landfills, most of which are not segregated – the rusted iron rebars are mostly never taken off the cement slabs and thus do not degrade easily, causing more pollution. In Mumbai, redevelopment is rife, as most of the apartments built over 40 years ago have reached the end of their lifespan. Across the city, three to four-story buildings are being demolished and replaced by high-rises. All of the demolition waste ends up in a landfill in the nearby villages or in the ocean, creating not only an eyesore but also increased pollution.
I am glad that because of my attempt to build a small cottage, one remote village in the Himalayas now knows the advantages of these traditional methods.
Several organizations in India are supporting and spearheading the move towards sustainable methods of construction that draw on traditional building techniques.
The experimental township of Auroville started in 1968 near the southern Indian city of Puducherry. In Auroville, they have experimented with various traditional types of construction, mixing them with modern amenities while also conducting workshops to teach people about the techniques.
The experimental township of Auroville started in 1968 near the southern Indian city of Puducherry. In Auroville, they have experimented with various traditional types of construction, mixing them with modern amenities while also conducting workshops to teach people about the techniques
In the bustling city of Bengaluru, alongside the highrise buildings, a company called Total Environment is building sustainable high-rises. They are taking small steps like using exposed hollow brick for the exteriors (avoiding cement, plaster and paint), stone flooring and integrating garden spaces even on the upper floors.
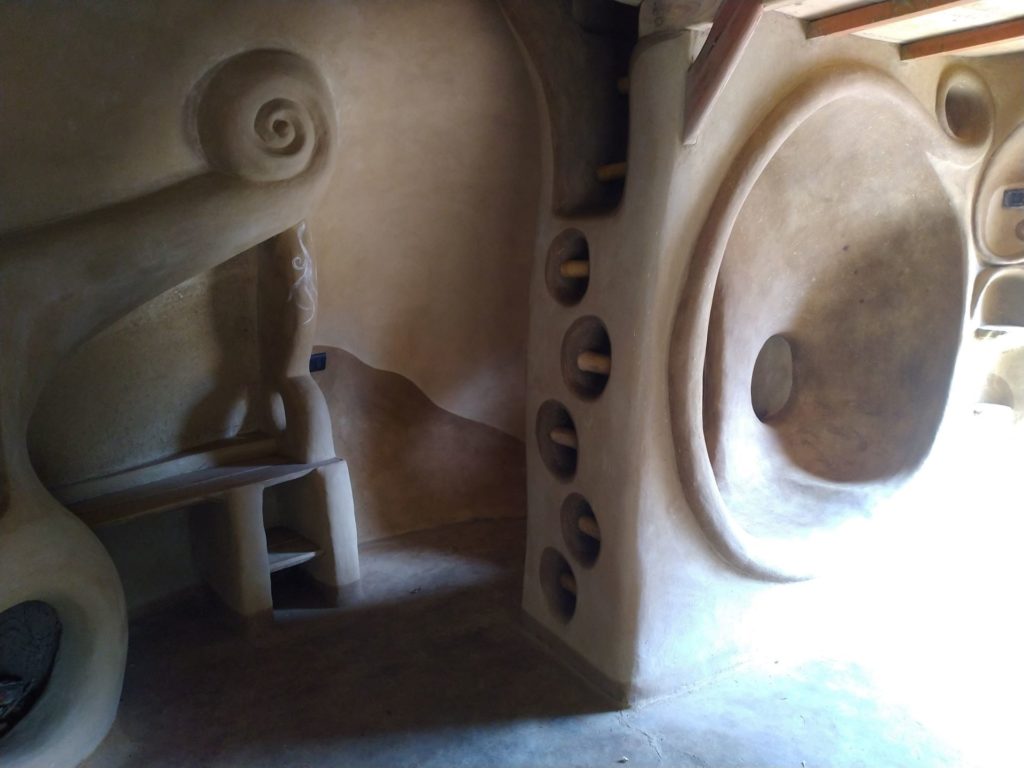
In a small town in Tamil Nadu is Thannal – an organization that builds mud houses and regularly conducts educational workshops. In a small village near Nainital in northern India, an organization called Geeli Mitti developed on an acre of farmland and focuses on creating awareness through workshops. They have a number of mud homes on the property which also have living roofs, causing them to blend into the landscape. They believe that unless you put your hands in the mud and understand its benefits and complications, you cannot build a mud home. The Indian National Trust for Art and Cultural Heritage, another NGO founded early in the 1860s, has been working on conserving heritage across India and has chapters for several cities with dedicated people working towards the conservation of traditional construction methods.
Companies like Earthblocks in Bangalore are mass-producing compressed stabilized earth blocks, which are essentially mud bricks, and can be used in construction just like regular fired bricks, making it easier to build a sustainable house.
Slowly but surely people are now choosing a breathable, long-lasting home that is comfortable to live in and looks appealing. Most of them start with farmhouses, and other homes that are away from the main city as sourcing high-quality materials in urban areas is a challenge. But the movement is underway, and while heading back to mud construction might be costlier in the beginning, it will provide sustainable, long-term benefits.
From being built with natural materials available locally to eventually degrading back into the same soil it came from, these houses depict the circle of life in its fullest.