The Biomimetic Hull
Inventors got their inspiration from nature to solve technical challenges for millennia. However, it is not as simple as it sounds, since highly complex biological structures cannot easily be copied technologically. Biomimetic solutions have enormous technical potential and collaborative projects continue to conduct research – also for shipping hulls.
Introduction
In the course of evolution, nature has developed a multitude of mature strategies to overcome all kinds of physical hurdles. Biomimetics tries to understand the underlying mechanisms of these biological phenomena and to transfer and translate them into technical concepts. Even though biomimetics is still quite young as a science, the basic idea has influenced technical inventions in the past as well.
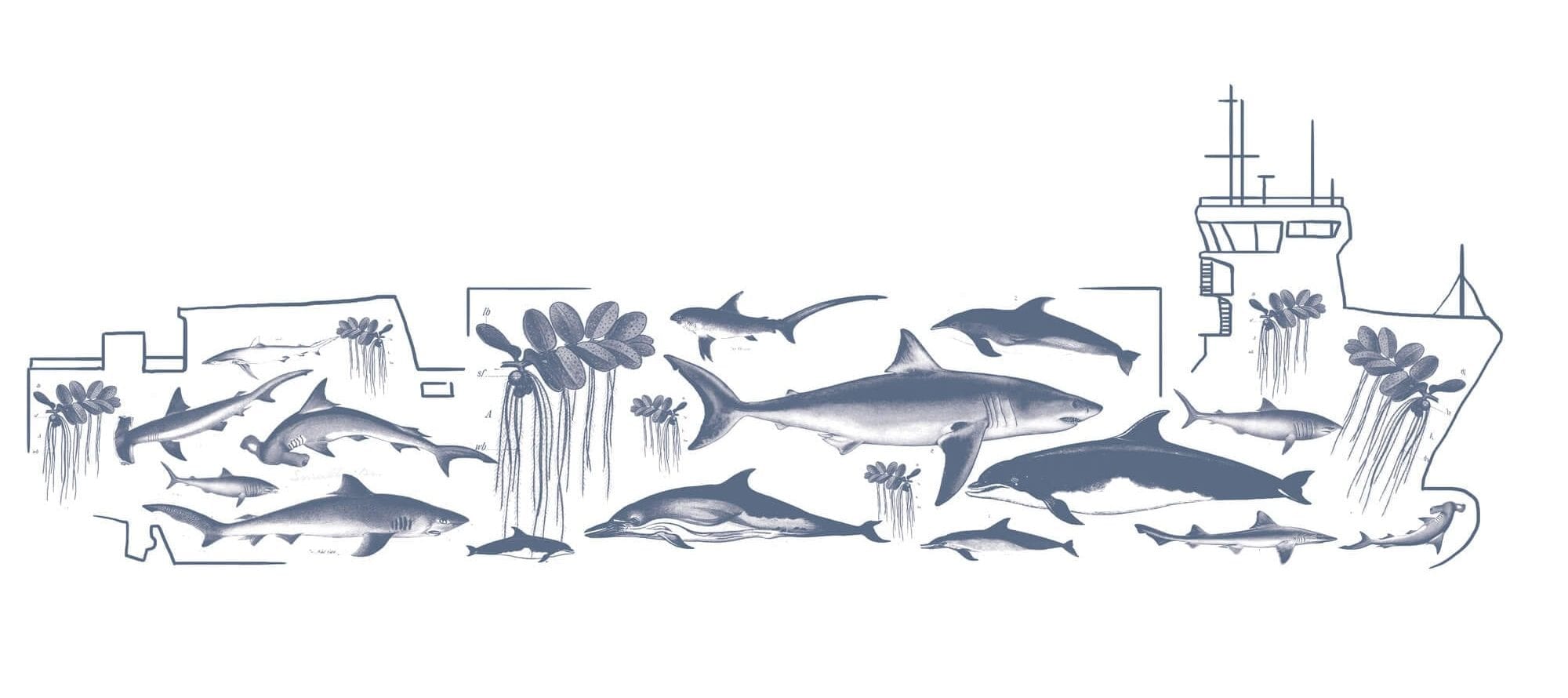
Leonardo da Vinci developed aircraft, helicopters and parachutes – the technical implementations of which were only prevented by the time in which he lived. The Swiss engineer George de Mestral got the idea for one of the first biomimetic products from his dog. After walks in the woods, he always had to take out burrs in his fur. When he looked at the holding mechanism more closely, he discovered the technical potential and patented the Velcro in 1951. Another biomimetic example is the lotus effect. The surface of the lotus plant can clean itself by combining microstructures and wax crystals. This effect was discovered in the 1970s. It has been used in paints, varnishes and sanitary facilities for about 20 years.
Even now in the 21st century, despite enormous scientific and technical progress and new possibilities in computer simulation and experimental technology, nature still forms the basis for numerous technical innovations. Bio-inspired technical innovations are developed with the most modern scientific tools and advanced, for example, in large international collaborative research projects such as the AIRCOAT project.
Biomimetics in fluid mechanics
Fluid mechanics – the science of the physical behavior of fluids and the flow around bodies – is ideal for biomimetic developments. Interactions between body surfaces and flowing media lead to forces that must be compensated by muscle power (in living beings) or drive power (in ships, cars, airplanes). Nature has developed many mechanisms to keep these forces (the flow resistance) and thus the energetic locomotion effort as small as possible.
In shipbuilding, innovative hull shapes lead to a steadily reduction of the so-called form drag. In return, however, the dominance of the remaining skin friction drag increased. This friction also increases with the steadily decreasing speed of ships (“slow steaming”) and causes increasing fuel costs. Innovative biomimetic concepts are therefore of great ecological and economic interest for ship-building.
Sharks and dolphins
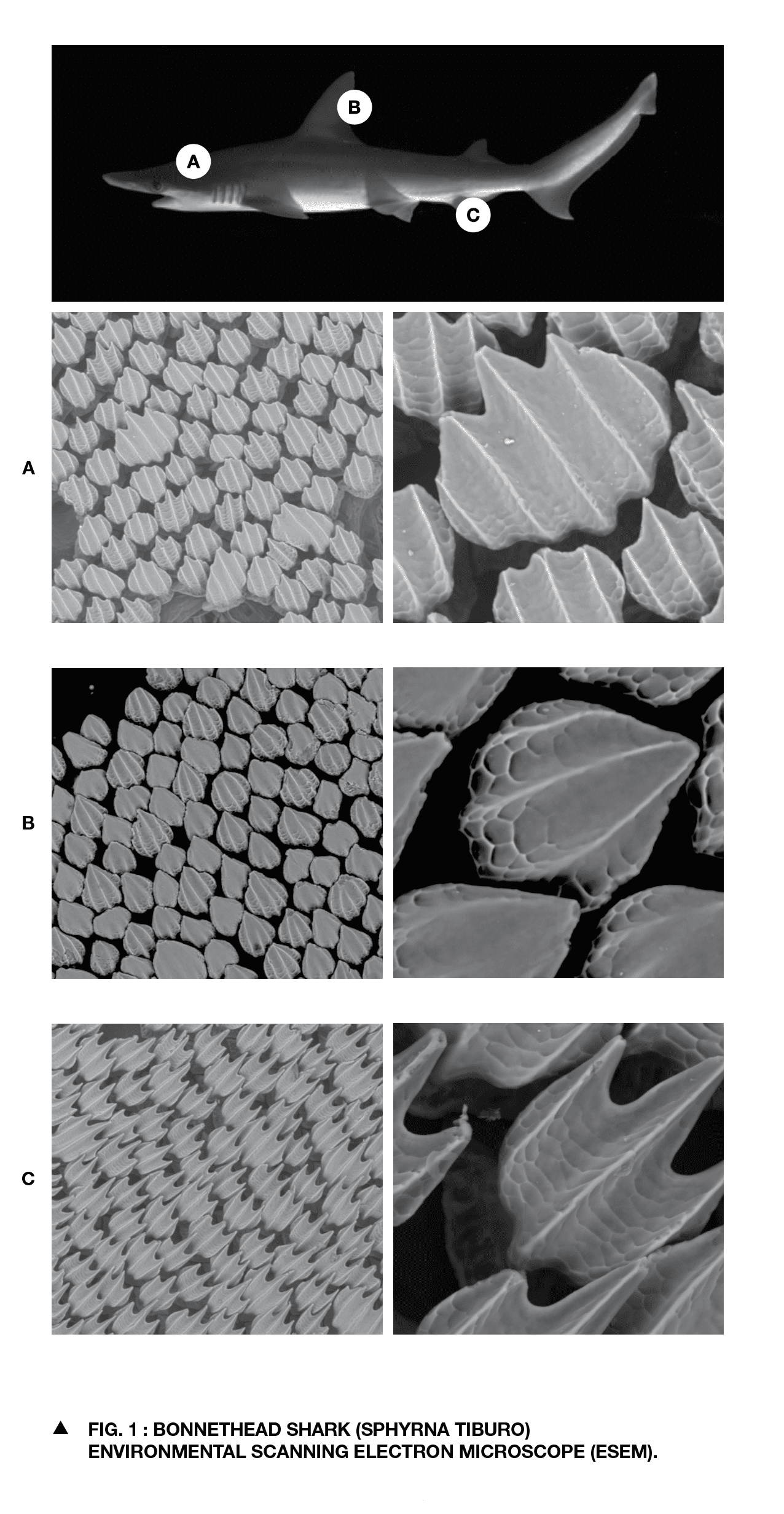
Shark skin is an established biomimetic approach to reduce frictional resistance. Its surface is covered with many tiny teeth, the so-called denticles, which have several grooves aligned in the direction of the flow (Fig. 1). Since a long time it is assumed that the denticles minimize hydrodynamic resistance. A valid method to check this was only found in 2012. Using a fin flapping robot, Oeffner & Lauder let the skin of two shark species oscillate elastically in the flow channel and demonstrated a 12% lower drag, compared to the same skin with removed denticles.
In the 1980s engineers invented Riblets inspired from shark skin, which possess fine ribs structures with sharp tips). Experiments in flow channels showed a 7% drag reduction. However, the application of Riblet foils on aircraft and ship hulls proved to be uneconomical, as the relatively low minimization of resistance was exceeded by increased maintenance costs.
Oeffner & Lauder found that the dynamic change in skin shape caused by the shark’s swimming movement is crucial for minimizing its drag. However, compared to the shark, a ship or airplane hull is rigid. Therefore, the functionality of the biological model can only be implemented to a certain degree. The technical effectiveness of biomimetic shark skin is thus limited.
Like the shark, the dolphin is also noticeable for fast movement with relatively low energy input. A closer look at its skin structure shows this is not due to the immediate surface texture, but to a deeper layer of dampening fat, which in addition to numerous other functions (such as thermal insulation and beneficial properties for wound healing) makes a decisive contribution to movement efficiency. The effect actually dampens interference waves occurring in the boundary layer and prevents the flow from a laminar to an energy-consuming turbulent state. Here, too, it is not primarily the dampening properties but the overall deformation behavior of the dolphin skin that are decisive – This was recently being investigated in the international joint research project FLIPPER in which the Hamburg Shipmodel Basin (HSVA) and the Technical University of Hamburg (TUHH) were involved.
Thinking out of the box
In addition to direct adaptation, biological models in technology can also perform other tasks that go beyond their actual natural function. This has the advantage that the biological model can be selected specifically according to the technical requirements and possible technical limitations are circumvented by highly complex biological structures. A current example is the Salvinia effect and the EU project AIRCOAT.
The surface of the floating fern Salvinia is equipped with a special micro- and nanostructure and chemical composition, which enables it to form a stable continuous air layer once, submerge under water. This effect has massive technical potential. Equipping a ship hull with a continuous layer of air, the ship would literally glide over the water and thus reduce energy use and carbon emissions.
Already on the market are refit devices that use a similar concept by injecting air bubbles to the water under the ship hull. This microbubble technology is an active air lubrication solution. Inspired by the Salvinia effect, nanotechnologist Prof. Thomas Schimmel from the Karlsruhe Institute of Technology (KIT) has developed a passive air lubrication solution. They could show that this artificial surface maintains an air layer under water for several years and initial frictional resistance experiments were promising.
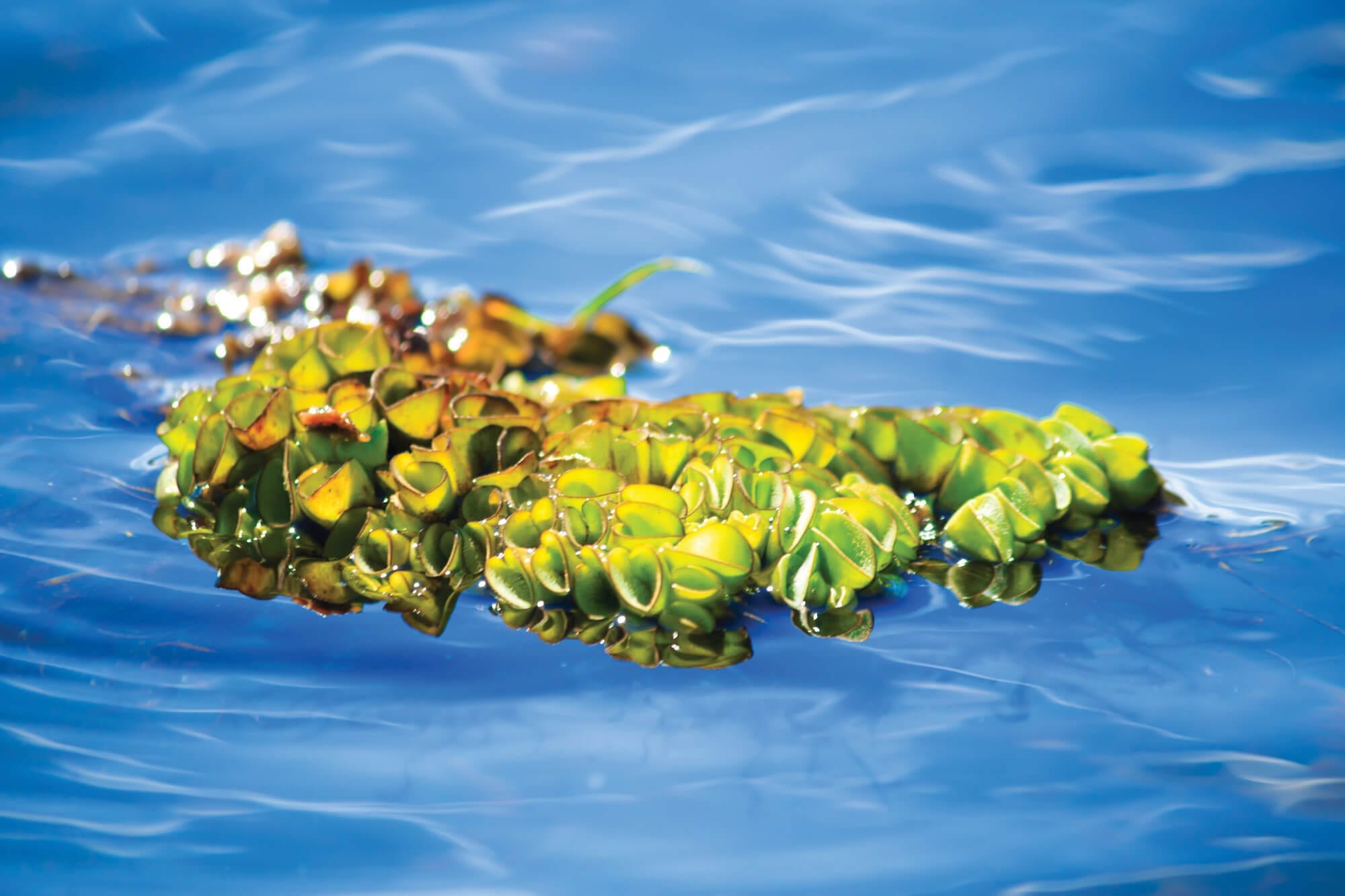
Biomimetics in shipbuilding
Fluid mechanic experiments and simulations of these biomimetic effects show significant drag reduction results. However, the examples also show that it is often only apparent at second glance which biomimetic mechanism is most opportune to use. This sometimes limits the technical transferability. In addition, surface coatings, especially in aircraft and shipbuilding, have to meet high durability requirements and there is a clear conflict of interests between aerodynamic and hydrodynamic resistance reduction and biological resistance. This is where the EU research projects eShark and AIRCOAT come in. The eShark project, which is due to finish 2018, targets to develop an environmentally-friendly, automatically-applied self-adhesive foil systems that have both anti-fouling properties and resistance-reducing effects. The 3-year AIRCOAT project, which started in 2018, combines this self-adhesive foil technology with the passive bio-inspired air lubrication technology to produce a game-changing hull-coating system. The project intends to validate its potential to reduce reducing frictional resistance, emission of pollutants and biofouling.
Some biomimetic effects contradict or complement each other in their effect and area of application – such as surfaces that are as smooth, rough or dampening as possible. While current research is more concerned with separate individual effects, a combination of techniques seems to be appropriate for technical applications, a task that must first be addressed in future research projects. Overall, a biomimetically-optimized hull could has a high potential to create a more sustainable water transport.