The Case for ‘Design-For-Recycling’ of Electrical Transformers
With their high economic value and substantial metal content, most medium-power transformers score highly in terms of recyclability. But not every type of transformer follows the same route at end-of-life. With increasing attention on the circular economy in European policy-making, recyclability is likely to become a decisive factor when choosing between different transformer types and design options.
Concepts like circularity, material efficiency and recyclability are quickly gaining ground in EU policy-making. But what does this mean for product design choices? When it comes to design-for-recycling, medium-power electrical transformers – used in electricity grids to change electric current from one voltage level to another – are an interesting case.
A first striking aspect of these transformers is the fact that they can remain in use for a very long time. Depreciation is typically over 40 years, but their actual lifetime is usually more than 50 years. While this is a major strength in terms of material efficiency, it also complicates the recyclability assessment at the design stage, since it is impossible to accurately predict where recycling markets, technologies and regulation will be 50 years from now.
Liquid-filled transformers set the example with about 75% of their material being re-used or subjected to first-grade recycling. The degree of circularity can be further enhanced by using copper for the high-voltage winding because the metal can be recuperated and recycled at high purity.
We have to make do with rough assessments, based on today’s market and technology. With this goal in mind, the Copper Alliance conducted an in-depth survey of the current state of transformer recycling, carrying out interviews at 20 stakeholder companies in various European countries. The data collected in the survey were processed and approved following the Delphi method. The survey revealed a sharp contrast between the end-of-life route of liquid-filled transformers and that of dry type units.
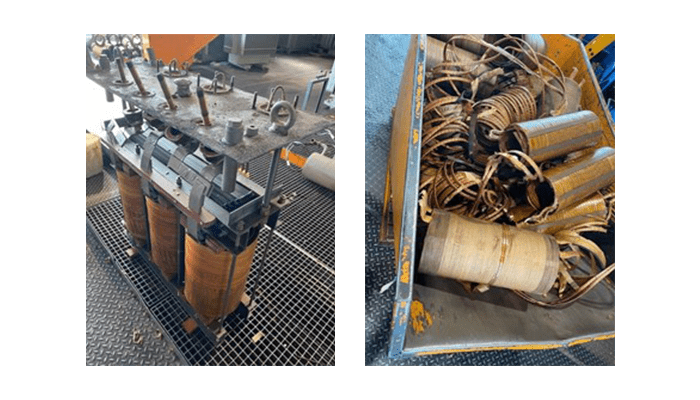
End-of-life liquid-filled transformers must be handled by certified recycling companies because oil in pre-1987 units might still contain man-made chemicals known as Polychlorinated biphenyls (PCBs) that are hazardous waste. The transformers are disassembled much in the same way as they were assembled. Much of the magnetic steel and mineral oil can be re-used, while more than 90% of the copper and structural steel is subjected to first-grade recycling, following an entirely circular route. Aluminium follows a second-grade recycling route, which means that it is downgraded only for use in second-life products for which this purity level is sufficient, such as building materials or non-electrical automotive parts. Only a tiny proportion of end-of-life transformer material is incinerated with heat recuperation (3-5%) or ends-up in landfill (1-2%).
Dry type transformers have their coils overmoulded with an epoxy or quartz resin, making recycling a major challenge. Separating this resin from the coils is time and energy consuming and not economically viable in the EU. It would require powerful machines for pre-cutting and several rounds of milling and grinding with high-powered shredders; even then, the metal could only be recuperated at low purity levels. Because of these barriers to recycling, the overmoulded coils are sold with other electro-mechanical scrap for export outside the EU. It is assumed that most of this ends up in India, where a low-paid workforce separates the resin (40-50%) from the aluminium coils (50-60%) in semi-automated processes. The recuperated metal is sold to foundries as low-grade scrap, while the resin elements end up in landfill.
This assessment demonstrates how liquid-filled transformers set the example with about 75% of their material being re-used or subjected to first-grade recycling. The degree of circularity can be further enhanced by using copper for the high-voltage winding because the metal can be recuperated and recycled at high purity. Dry type transformers, in contrast, illustrate how failure to take account of separability at the design stage can lead to a problematic end-of-life process.
The application areas of the two types of transformers partly overlap. Until now, circularity has seldom been a decisive factor in making the choice. With increasing attention around the different aspects of the circular economy in business and policy-making, this is likely to change now.