Designing for Disassembly Turns Waste into Worth
Designing buildings for disassembly lets them retire gracefully, leaving assets behind, not waste.
In an era where sustainability is paramount, designing buildings for disassembly is gaining traction. This approach ensures the easy deconstruction of structures, allowing materials to be reused or recycled, thereby reducing waste and environmental impact. Think of it as giving buildings a graceful exit strategy – like a well-planned retirement, but for bricks and mortar.
The case for disassembly
Traditional construction methods often result in buildings that are difficult to dismantle, leading to significant waste when demolishing them. Designing for disassembly (DfD) addresses this issue by creating buildings that can be taken apart systematically.
For example, NASA’s Sustainability Base was designed with disassembly in mind, allowing for the recovery and reuse of its components. This approach conserves resources and reduces the construction industry’s carbon footprint. It’s like building with LEGO, but on a grander scale without risking stepping on a rogue brick.
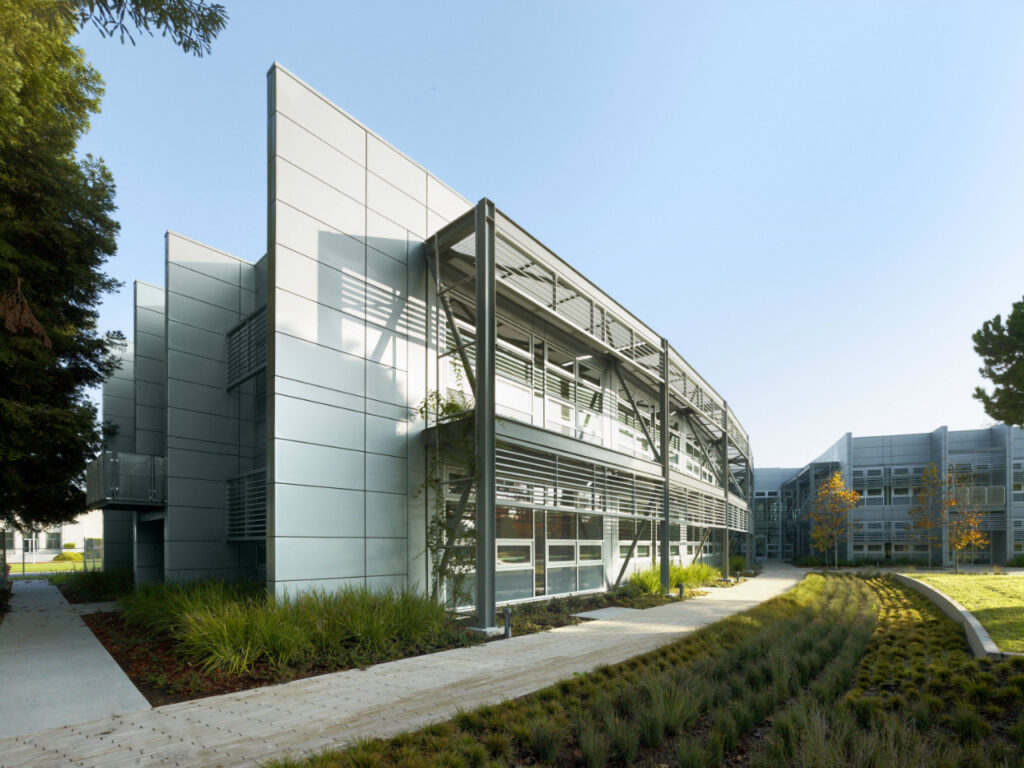
Lighter on the environment and your wallet
DfD has a positive impact on the environment. By reusing materials, we can significantly reduce the demand for new resources and decrease energy consumption and the emissions associated with producing new building materials. For instance, Arup’s Circular Building Prototype was designed for easy disassembly and its materials to be reused, helping to minimise waste and reduce environmental impact. Additionally, DfD sends less waste to landfills, which is a critical concern given the limited capacity of these sites. Imagine a world where buildings are like IKEA furniture – easy to take apart and reassemble without the confusing instructions.
DfD is not just environmentally beneficial; it also makes economic sense. The ability to reuse materials can lead to substantial cost savings. For instance, high-quality materials such as steel and timber can be salvaged and repurposed, reducing the need to purchase new supplies. Furthermore, the resale value of reusable materials can provide an additional revenue stream for developers. It’s like finding out your old comic book collection is worth a small fortune – who knew those materials could be so valuable?
What does the future of material resale look like?
Looking ahead, buildings designed for disassembly today could become treasure troves of valuable materials in the future. Imagine a scenario where the steel beams and timber from a deconstructed building are resold or reused in new constructions.
DfD saves money while creating a sustainable cycle of material use, much like investing in a vintage wine collection that only gets better (and more valuable) over time.
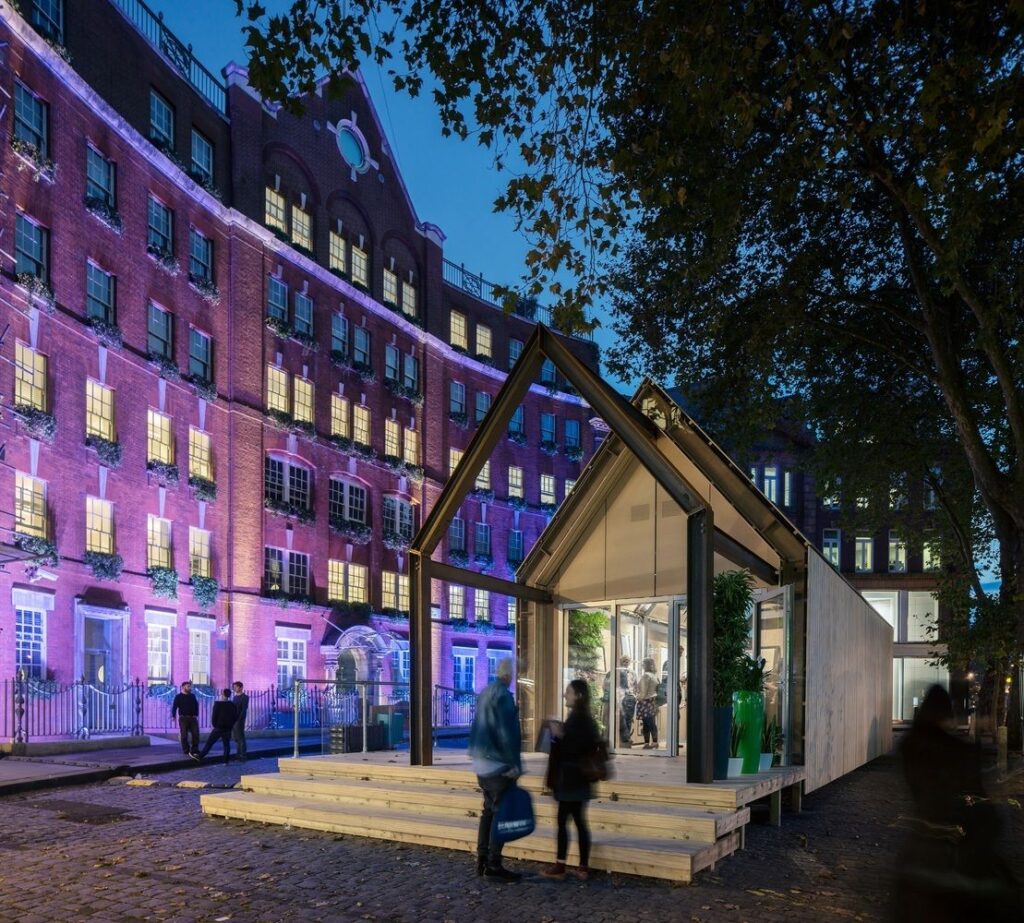
Challenges and solutions
Despite its benefits, DfD faces several challenges. One of the main obstacles is the industry’s hyper-focus on reducing embodied carbon over waste.
While important, selecting materials with lower embodied carbon (concrete vs. steel) provides little opportunity for future deconstruction potential. In addition, initial cost plays a role, as designing buildings for disassembly can be more expensive than traditional methods. However, these costs are offset by long-term savings tied to reuse and the potential resale of materials. Another challenge is the lack of standardised guidelines and regulations for DfD. To address this, governments and industry bodies must develop clear standards and provide incentives for adopting DfD practices. Cities like Portland, San Antonio, and Milwaukee have deconstruction ordinances that can guide other cities. Encouraging others to embrace deconstruction is like convincing people to eat their vegetables – it might be tough at first, but the long-term benefits are undeniable.
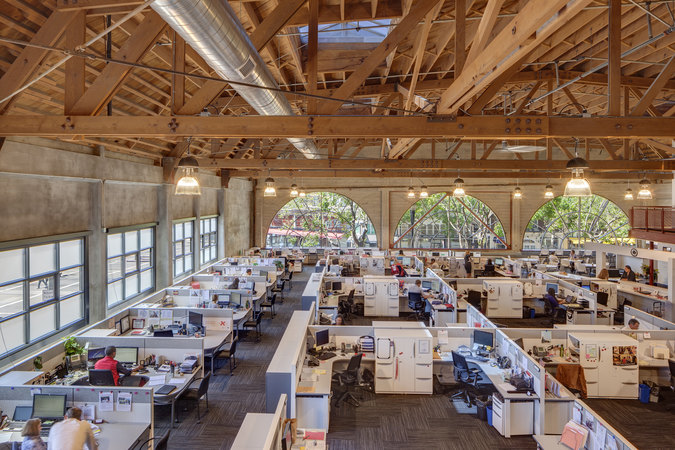
Recommendations for implementation
To promote the widespread adoption of DfD, several actions can be taken:
- Policy Support: Governments should introduce policies that encourage DfD, such as tax incentives for developers who adopt these practices.
- Education and Training: Industry professionals must be educated about the benefits and techniques of DfD. This can be achieved through workshops, seminars, and inclusion in architectural and engineering curricula.
- Research and Development: Continued research into new materials and construction techniques that facilitate disassembly is essential. Innovations in this area can make DfD more cost-effective and practical.
- Collaboration: Collaboration between architects, engineers, and contractors from the outset is crucial to ensure that DfD principles are integrated into the design and construction process.
Designing for disassembly is a forward-thinking approach aligning with the principles of sustainability and resource efficiency. By adopting DfD, we can create buildings that serve their purpose during their lifespan and contribute to a circular economy by providing valuable materials for future use. It is time for the construction industry to embrace this concept and ensure that every building comes with an exit strategy. After all, even buildings deserve a dignified retirement.